Know Your Watches: What Is Guilloché?
Guilloché, a technique used to create intricate, repetitive patterns on watch dials and other surfaces, is one of the most revered forms of decoration in luxury watchmaking. Similar to the textured brush strokes on a canvas, guilloché has been used for centuries, adding depth and a sense of wonder to high-end timepieces. Painstakingly done by hand, the entire process is a testament to the watchmaker's skill, precision and artistic abilities imparting beauty to a technically sound timepiece. But what makes this age-old technique so coveted in modern watchmaking? How has this technology evolved over the years and where does it stand today? To know this, we need to first understand the origins of guilloché.
A brief history of guilloché
Guilloché as a decorative art form can be traced back to the 16th century, though it gained significant prominence in the 18th century. The term "guilloché" comes from the French word "guillocher," meaning to engrave or carve in intricate patterns. While the origins of the technique are not attributed to a single inventor, it is believed that the earliest known example was a timepiece with an engine-turned case created by Pierre Duhamel in Geneva in 1680.
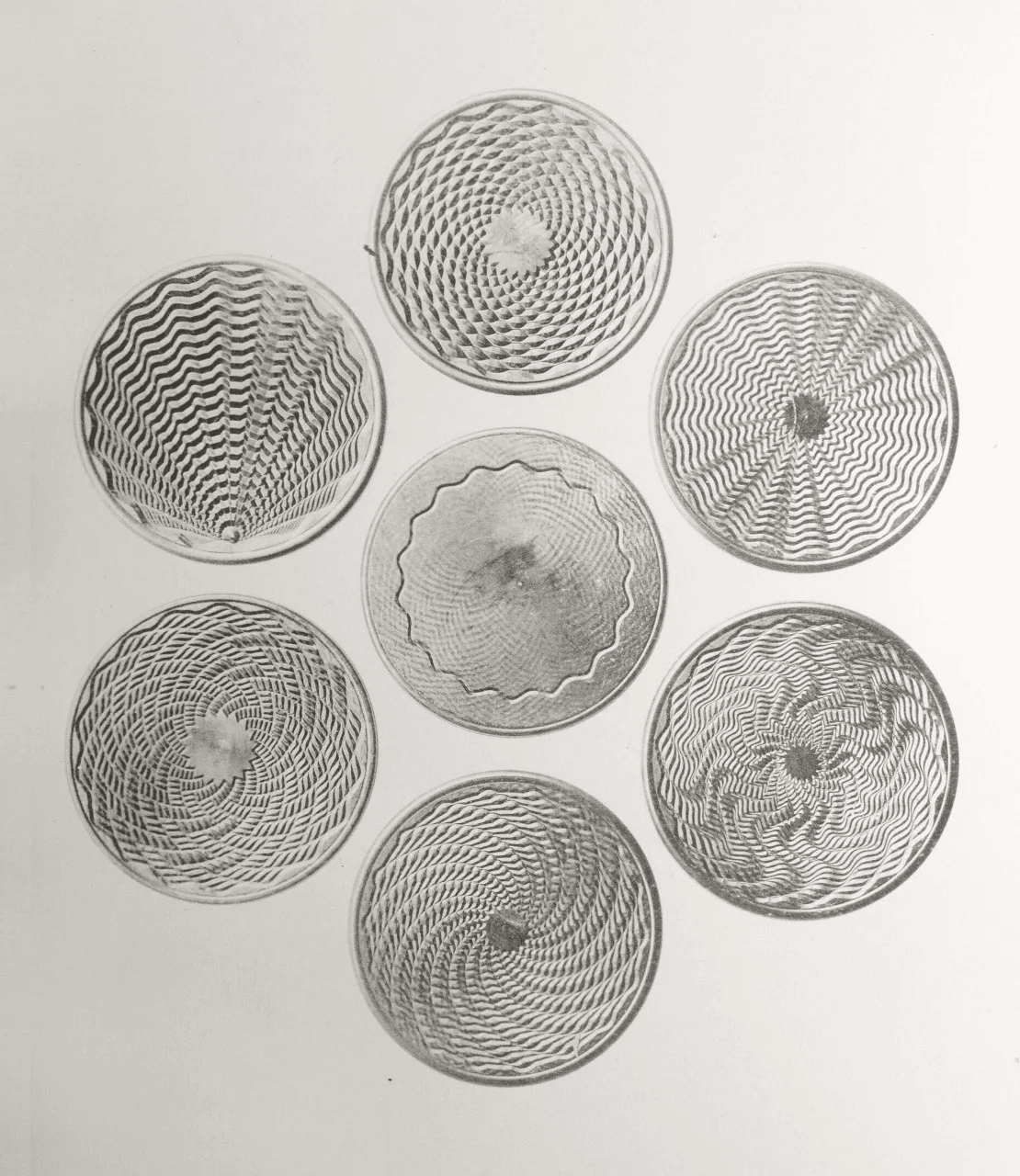
One of the earliest uses of guilloché was on precious metal objects, such as jewellery boxes, serving trays and other decorative items where artisans would engrave repetitive patterns to enhance the beauty and value of the pieces. These engraved patterns were not only visually appealing but also required an immense amount of skill and precision. As the technique evolved, it was adopted by watchmakers to adorn the dials, cases, and movement components of high-end watches.
Mechanizing the art
While early guilloché patterns were created by hand, the technique was significantly enhanced by the invention of engine-turning machines, also known as rose engines and straight-line engines. These machines, introduced in the late 18th and early 19th centuries, allowed artisans to create more precise and intricate patterns with a greater level of consistency.
But how do these machines work? Using a system of gears and cams to guide a cutting tool along a pre-programmed path, the tool engraves the surface of the watch dial or case, creating the desired pattern. Rose engines produce circular patterns, while straight-line engines create linear patterns. The rose engine cutter is angled at different degrees, such as 90, 100, 110 or 120 degrees. The method of carving is a method of pressing in, cutting and removing the excess. The product will have a shimmery texture.
Some brands employ more cost effective methods such as computer numerical control (CNC) machining and hydraulic stamping for their entry level and mid-range watches. CNC machining utilizes a tool that is turning, leaving distinct milling marks, while stamping involves material deformation which doesn’t produce a sharp surface. The combination of these machines allows artisans to produce a wide variety of guilloché designs, from classic wave patterns to more complex motifs like sunbursts and clous de Paris (hobnail).
The advent of engine-turning machinery revolutionized the guilloché process, making it more accessible to watchmakers and allowing for a greater variety of designs. A good tip to ascertain whether the guilloche is done by hand or CNC is when patterns are large and rough, they can be done with CNC, but when it gets small and fine, it can only be made by hand. Despite the mechanization, the technique still requires a high level of skill, as the artisan must carefully calibrate the machine, choose the correct pattern, and maintain steady pressure to ensure a consistent engraving.
Painstaking precision
In hand-engraved guilloché, the artisan uses a burin, a type of chisel, to manually carve the design. This method requires exceptional control and precision, as even the slightest mistake can ruin the pattern. Hand-engraved guilloché is considered the pinnacle of the art form, as it showcases the artisan’s skill and expertise making it one of its kind. Engine-turned guilloché, while still requiring a high level of skill, is more consistent and precise due to the use of machinery. However, the process is far from automated; the artisan must carefully set up the machine, guide the cutting tool, and monitor the process to ensure the pattern is engraved correctly. The machinery used in engine-turning is often vintage and requires regular maintenance to remain functional.
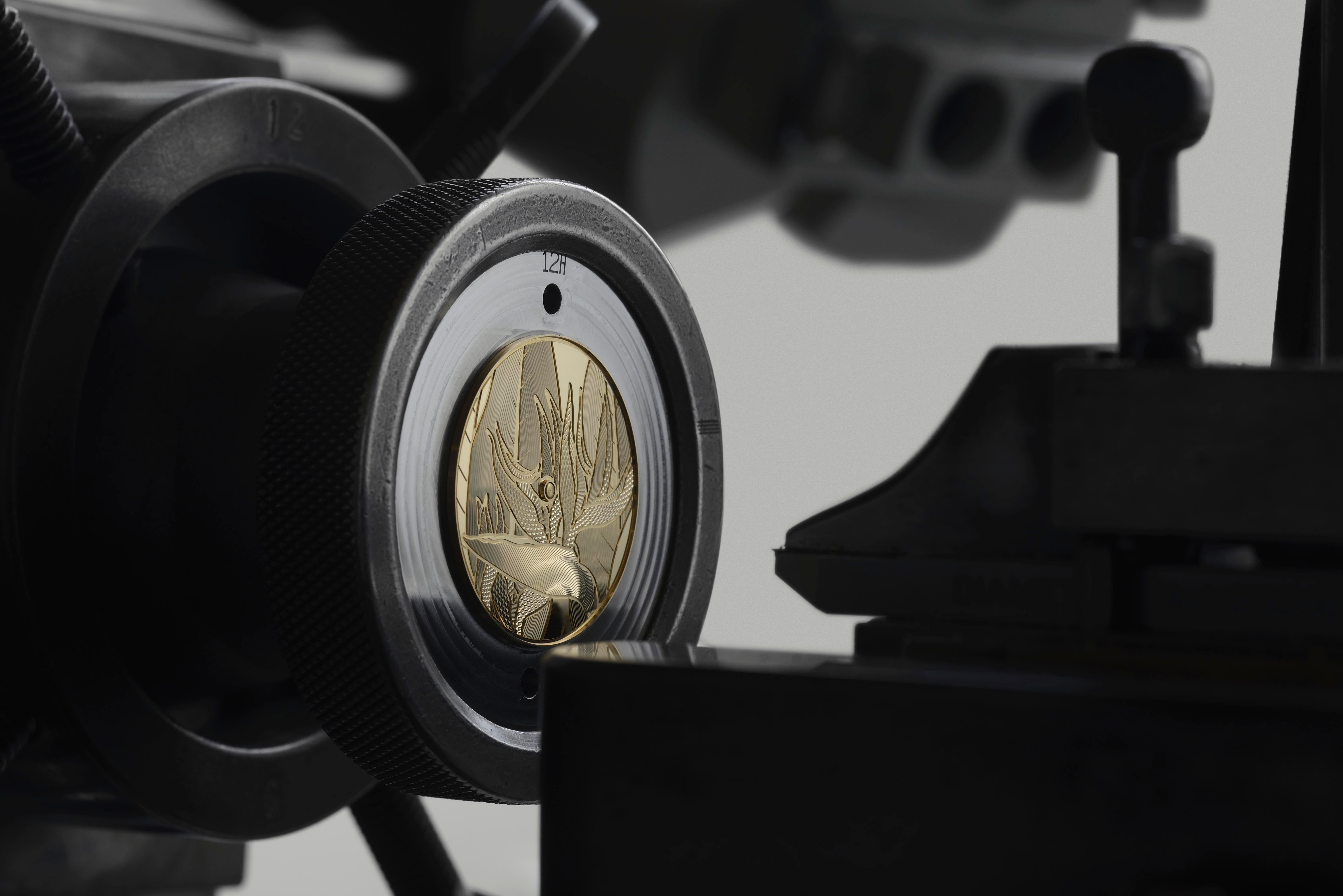
The most challenging aspect of the craft lies in possessing a complete understanding of the machine. Work holding and preparation of the cutting tools are crucial to success, and this can only come with experience. There are so many variables in engine turning. The engraving tool needs to be mirror polished and sharp, the rosettes or pattern bars that the pattern guides off needs to be mathematically and functionally flawless, the guillocheur needs to keep complete concentration with cutting and indexing the machine correctly, and lastly be open-minded to correct any errors and mistakes.
Elevating craftsmanship
Guilloché decoration has long been associated with luxury, and its use in watches is no exception. Watchmakers recognized the appeal of guilloché not only for its aesthetic qualities but also for the way it reflects light, creating a dynamic and captivating effect. The technique adds a sense of depth to watch dials, making them appear almost three-dimensional.
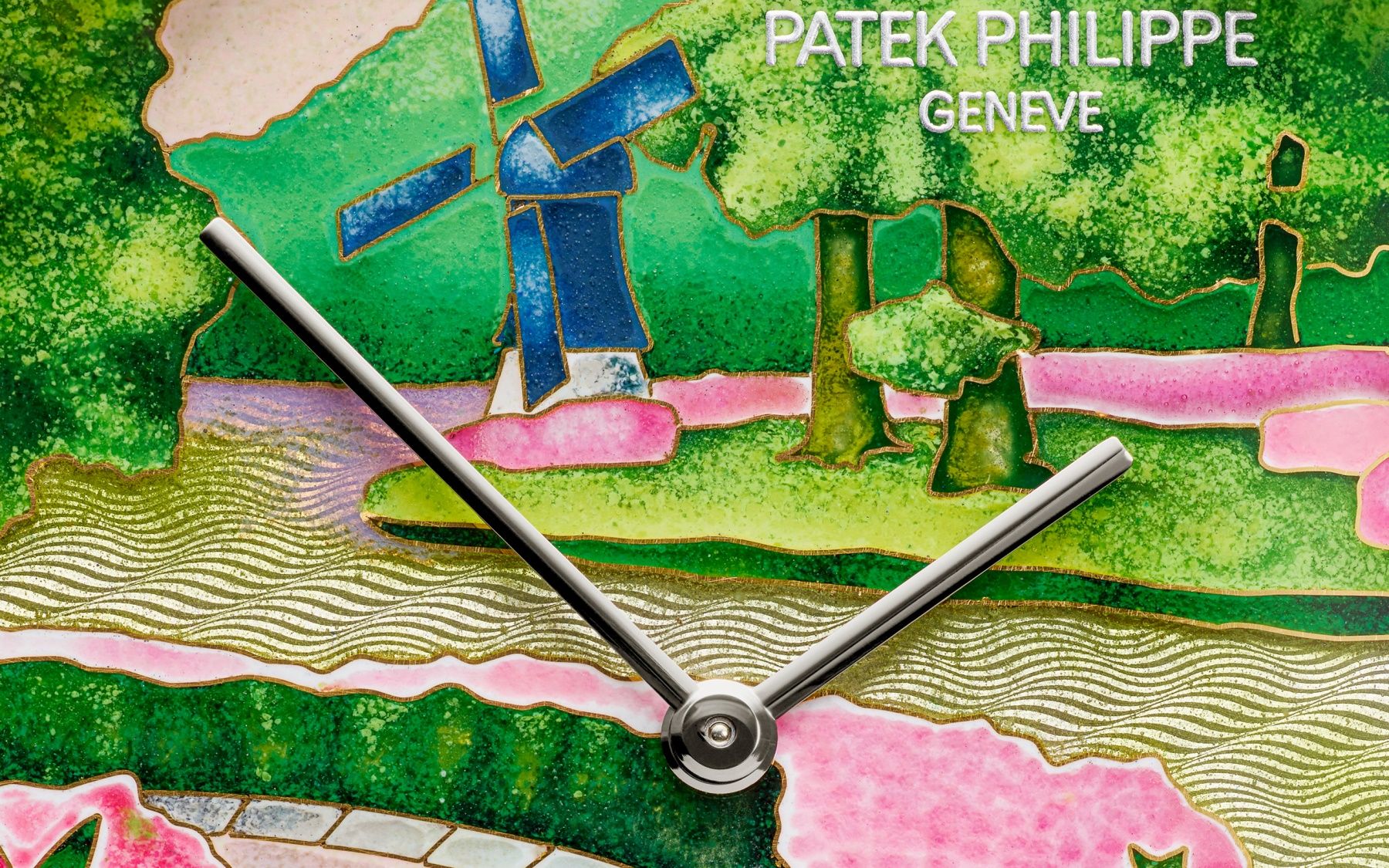
Some of the most renowned watchmakers in history have incorporated guilloché into their timepieces, elevating them to the status of works of art. One of the earliest watchmakers to popularize guilloché in watches was Abraham-Louis Breguet, the legendary Swiss watchmaker and founder of the Breguet brand. In the late 18th and early 19th centuries, Breguet used guilloché on the dials and cases of his watches, helping to establish the technique as a hallmark of luxury watchmaking. Today, the Breguet brand continues to use guilloché in many of its high-end watches, carrying on the tradition started by its founder.
Another iconic watchmaker that has embraced guilloché is Patek Philippe. Known for its exceptional craftsmanship and attention to detail, Patek Philippe often uses guilloché to add a touch of elegance and refinement to its dials. The brand’s use of guilloché has helped solidify its reputation as one of the top names in luxury watchmaking. In addition to Breguet and Patek Philippe, other high-end brands such as Vacheron Constantin, Jaeger-LeCoultre, and Audemars Piguet have also incorporated guilloché into their watch designs, giving their timepieces a unique aesthetic.
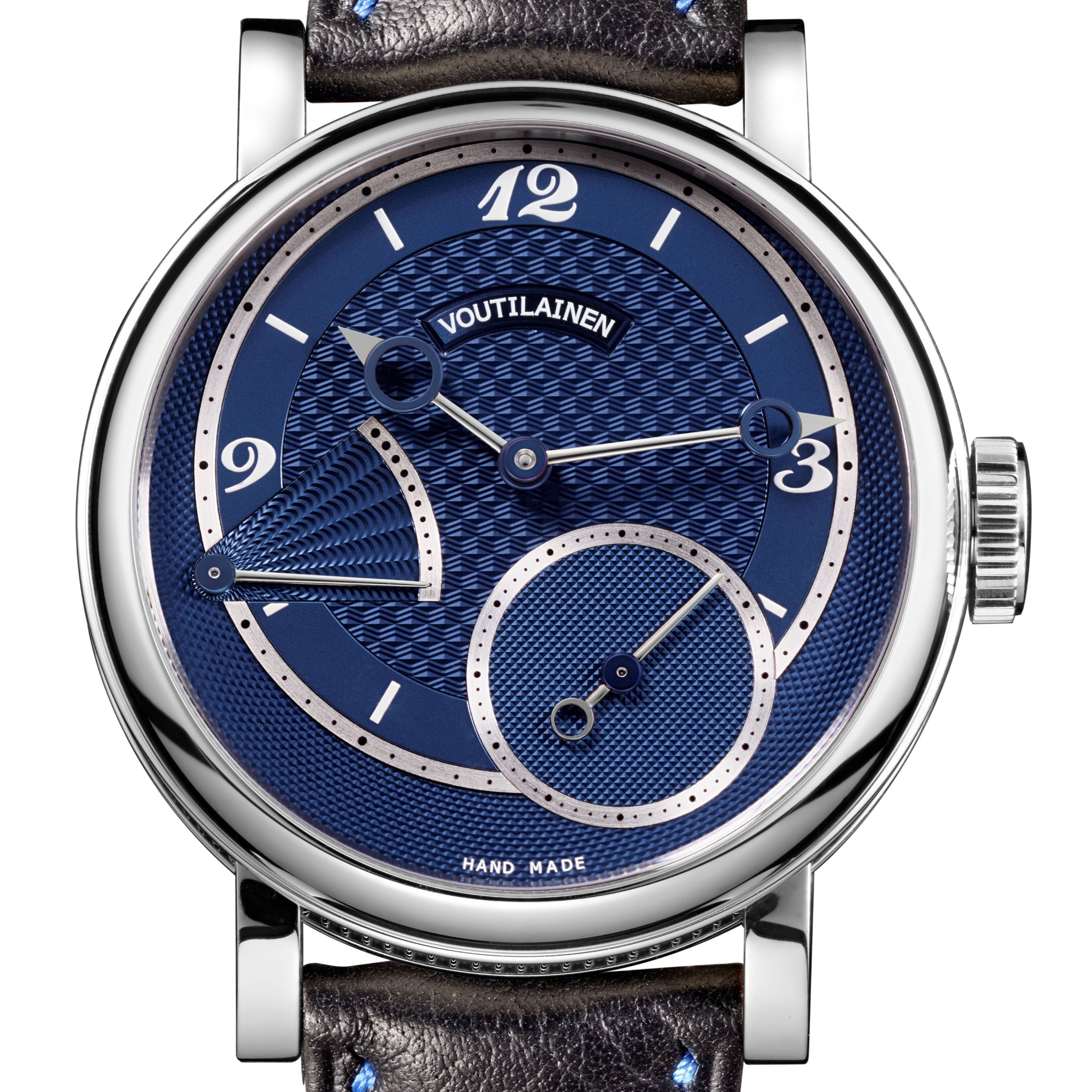
For collectors and enthusiasts, guilloché is a symbol of craftsmanship, and attention to detail. A guilloché dial speaks to the time and effort that has gone into creating the watch, making it a prized possession for those who appreciate fine watchmaking. The human element used to create these designs make it a wearable work of art evoking the wearer’s affinity for handmade luxury. Whether hand-engraved or engine-turned, guilloché remains one of the most beautiful and enduring forms of decoration in the world of luxury watches.
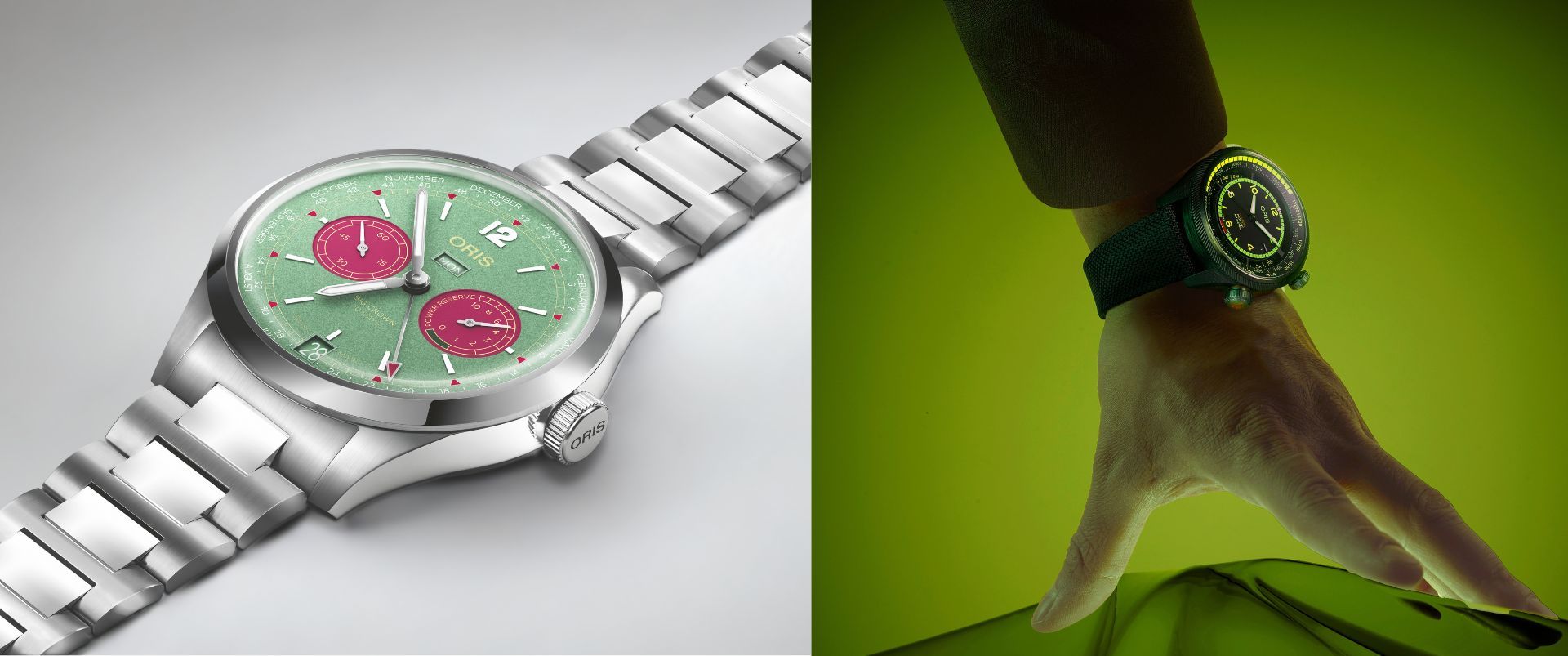
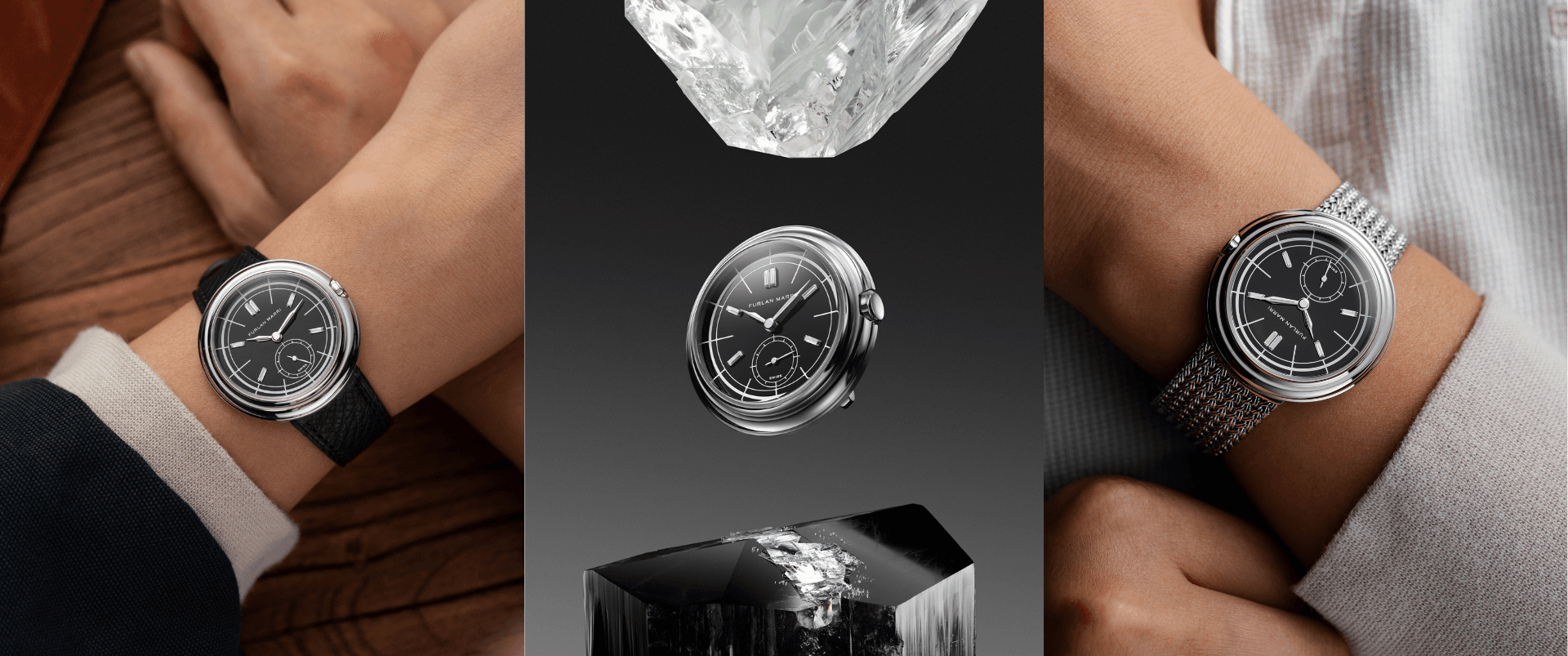
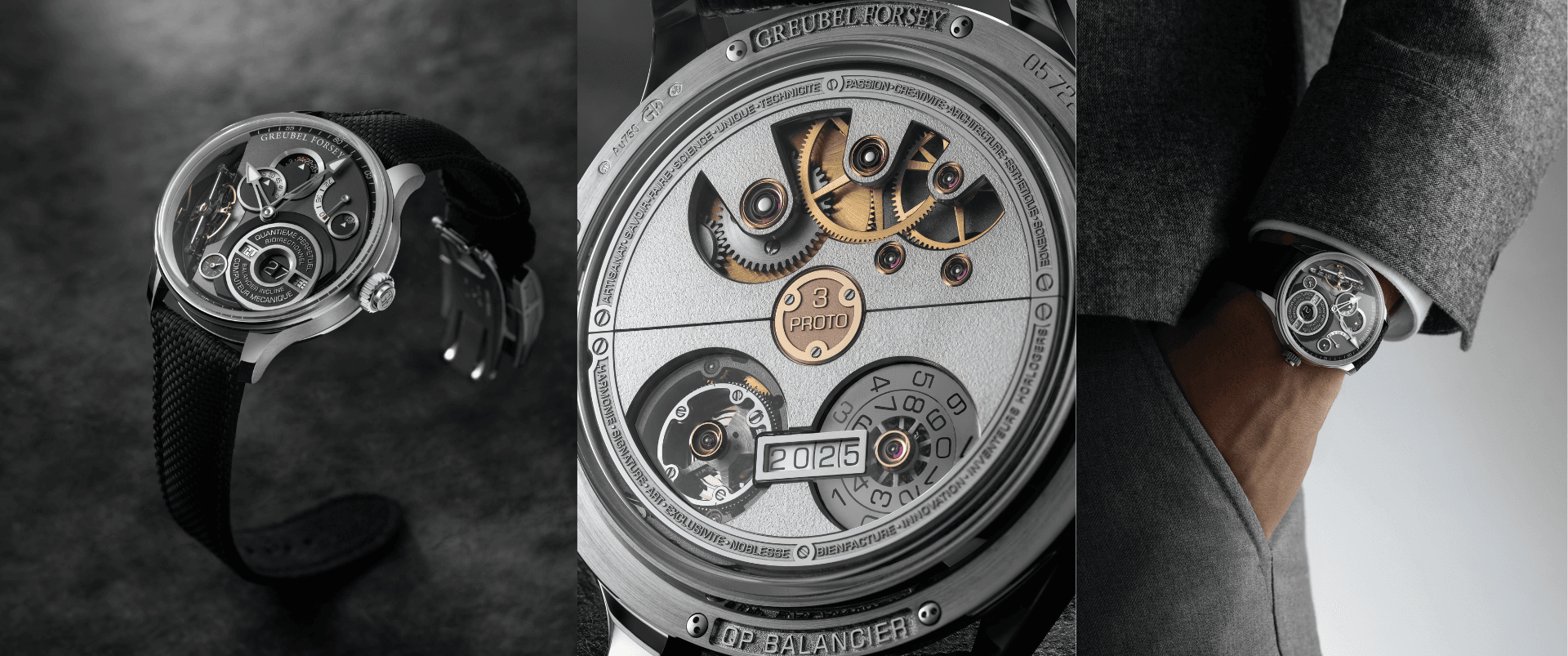
No articles found