Born From A Dare: The Extraordinary Journey of MING Project 21 Horological Omakase
It began with a dinner. A warm evening in Singapore, 2023, surrounded by collectors and friends, when a simple but audacious challenge was thrown across the table. "Ming, if you could design a watch purely for yourself—no market constraints, no compromises—what would it look like? And if you did, would you make one for us too?" For Ming Thein, founder of MING, this was both an intriguing and perplexing question. After all, every MING timepiece is born from passion—if they wouldn’t wear it themselves, they wouldn’t make it. Yet, commercial realities still influence decisions: an ultra-thin, hand-finished movement in an entry-level watch is an impossibility. Some ideas, though exciting, simply don’t make sense for production.
Act I: The Challenge
Ming pondered. "A big part of design is experimentation. Even if it turns out to be impossible, pushing the boundaries of ‘what if?’ is essential. There are ideas I love that never see the light of day because they’re too niche or too unconventional. But this time... this time, I would let my imagination run wild."
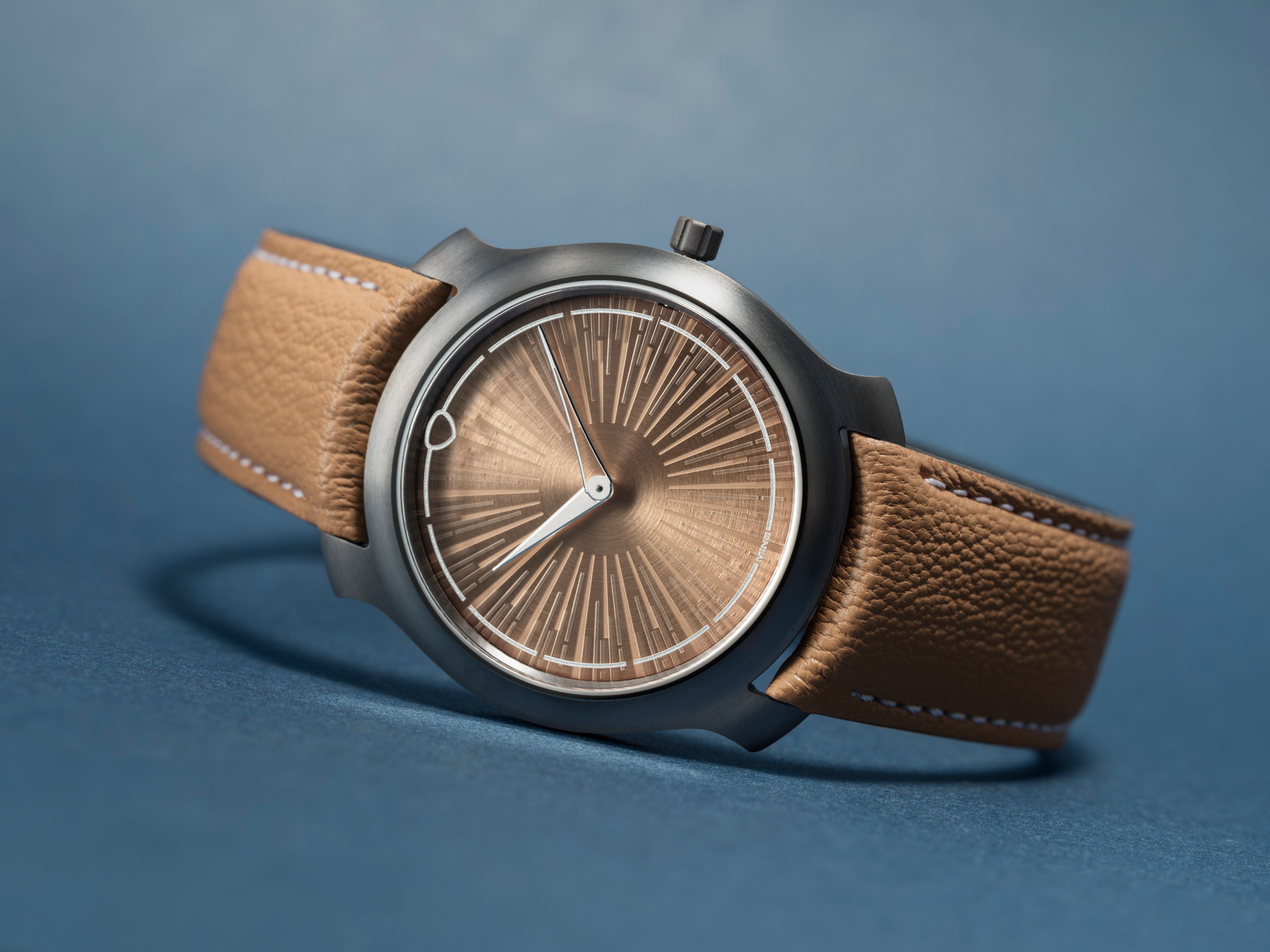
And so, he set out on an extraordinary journey—a watch without compromise, without preconceptions. But with such an unknown path ahead, there was no way to present a final design before seeking commitment. The only certainty was a price cap, a delivery estimate, and a movement new to MING. Ten bold collectors placed their trust in Ming’s vision. A horological omakase began.
Act II: Design & Engineering
At the heart of this experiment lay a movement of historical significance—the legendary Frederic Piguet 21. Introduced in 1925 and produced for nearly a century, it remains one of the thinnest mechanical movements ever made at just 1.75mm. It has powered some of the finest watches from Patek Philippe, Audemars Piguet, Vacheron Constantin, Jaeger-LeCoultre, IWC, Blancpain, and Cartier. For years, Ming had dreamed of building a watch around it. Now was his chance.
But a small movement demands a proportionate case. And while MING has always prioritized visual presence over sheer dimensions, anything smaller than 38mm would be truly niche. Ming settled on 35mm—teetering between modernity and vintage charm. "I wanted it to wear large despite its size, so I pushed the dial elements to the outermost edge, framed by the narrowest of bezels. It had to be ultra-thin yet robust, with 50m water resistance and excellent torsional rigidity."
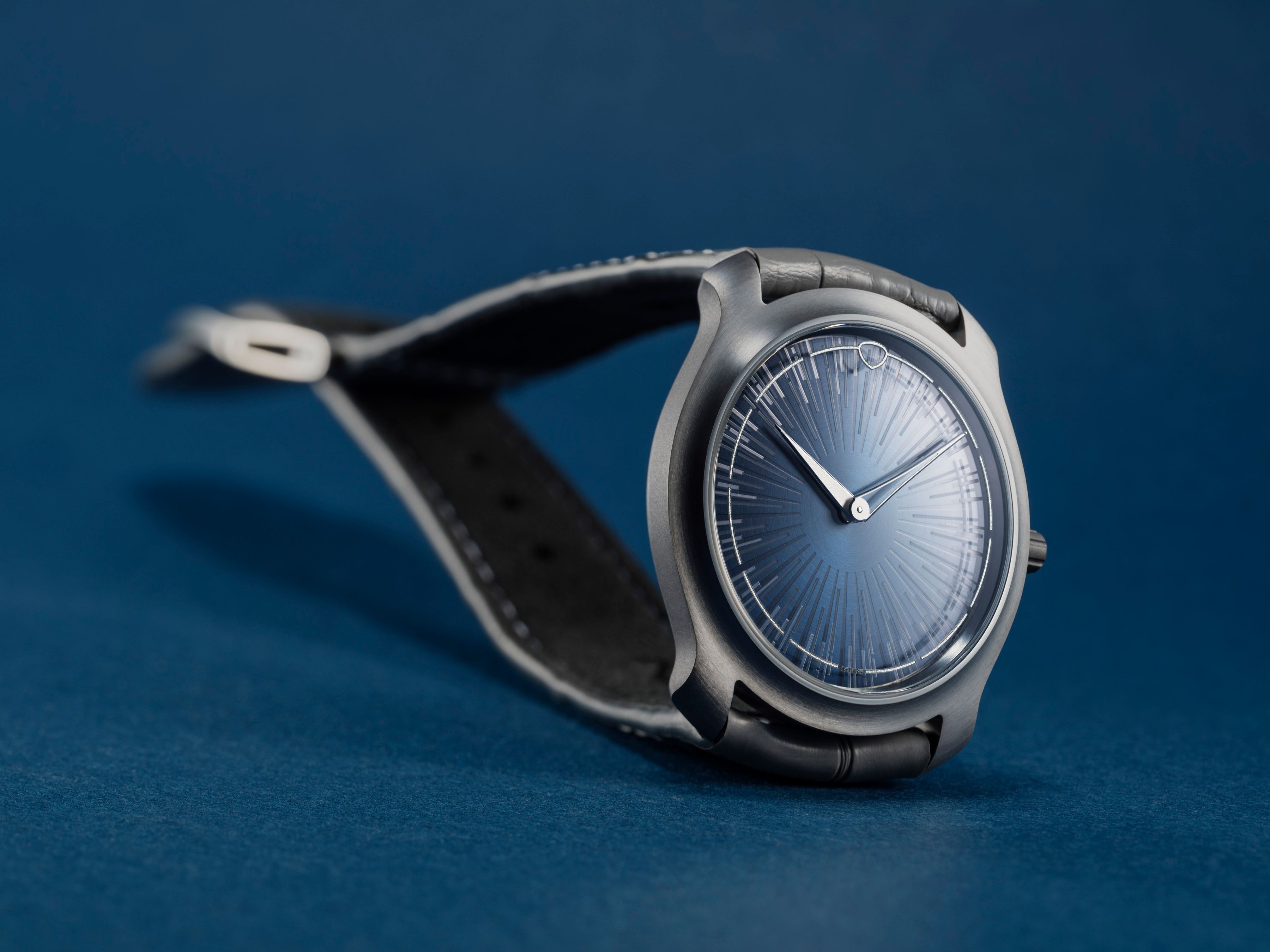
However, a small case runs the risk of feeling insubstantial. Ming’s answer? The opposite approach. He designed a case that would be as dense and heavy as possible, fully enclosing the movement without a separate bezel. The material? Tantalum—one of the most exotic and difficult metals to machine, chosen for its luxurious weight and dark luster.
"I wanted three distinct finishes—mirror-polished on the rehaut edge, fine circular brushing on the concave bezel, and sandblasted sides flowing seamlessly into the caseback. Every contour would curve in at least one direction, sometimes two. Even the caseback wasn’t purely circular but had a subtle trapezoidal protrusion to accommodate the crown tube. The complexity of machining it was borderline madness."
Act III: It Takes a Village
A design this ambitious demanded the best craftsmen in the world. And for the case, Ming turned to none other than Joshua Shapiro—renowned watchmaker, co-founder of the Alternative Horological Alliance, and a master of machining. His team in Los Angeles took on the near-impossible task of producing and finishing the tantalum case, down to the delicate, multi-finished 3.5mm crown.
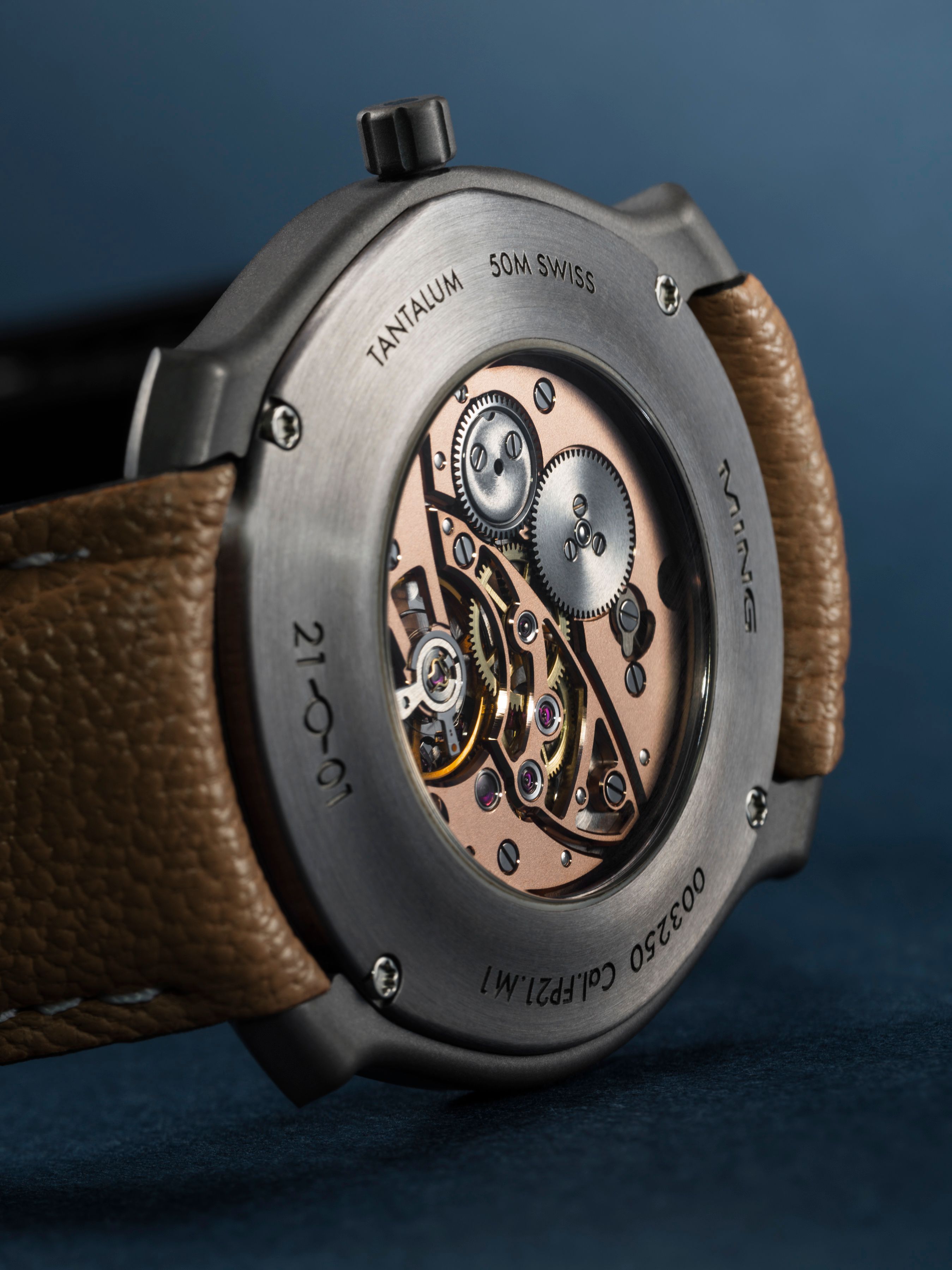
"Machining tantalum is always a challenge," Josh admits. "And Ming’s designs? They are always beautifully intricate and fiendishly difficult. But the result? We believe a tantalum case like this has never been made before."
Ming’s pursuit of perfection didn’t stop at the case. The Frederic Piguet 21 movement was reimagined with completely new bridges. One, in titanium, was skeletonized to reveal the gear train and color-matched to the dial, while others featured polished anglage and fine sablage in keeping with MING’s signature finishing. Collaborations with TitAl SA and Mathis Horlogerie brought this vision to life.
The dial was an equally radical endeavor. Despite the ultra-thin profile, it was actually composed of two layers: a straked brass plate, just 400 microns thick, milled with delicate textures and coated in CVD. Floating above it was a fused borosilicate layer by FEMTOprint, carrying a multi-dimensional pattern. The indices were etched directly into the external sapphire crystal, while the skeletonized hands were polished to perfection. For the first time in MING’s history, there was no luminous material—Project 21 would remain forever in the shadows.
"Every design decision was a study in contrasts," Ming reflects. "Project 21 is visually thin yet surprisingly heavy; it looks small but wears large; it feels vintage but is only possible thanks to modern technology. It is the most finely tuned expression of balance we’ve ever created." After months of painstaking craftsmanship, the ten bespoke pieces were delivered to their collectors. And now, MING is ready to share this masterpiece with a few more enthusiasts.
A Final Chapter: A Limited Release
For those who missed the omakase, MING presents a special edition of the Project 21: a 15-piece limited run featuring a 5N rose gold-coated dial and a matching movement with 5N rose gold-coated bridges. For a watch that began as a challenge among friends, Project 21 has become something far greater—an exploration of possibility, a testament to craftsmanship, and a rare glimpse into the mind of a watchmaker unbound by convention.
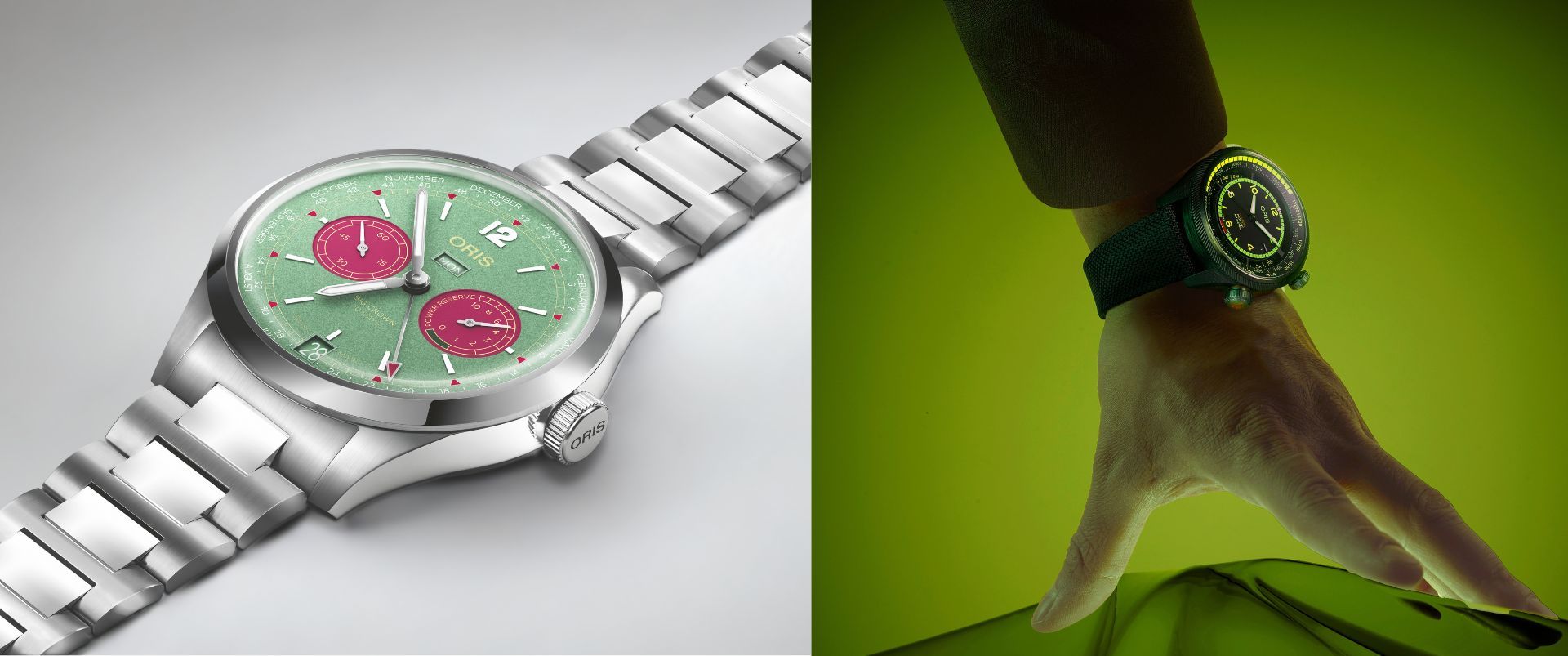
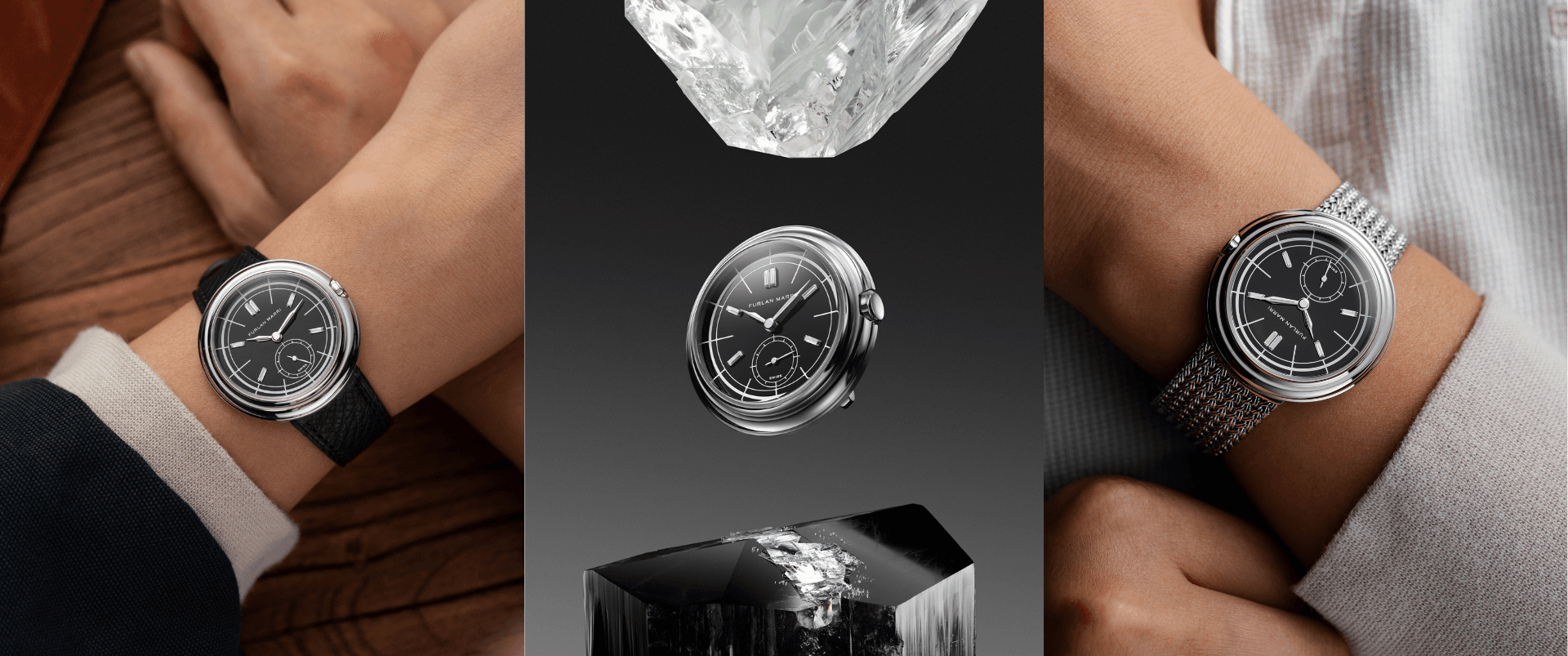
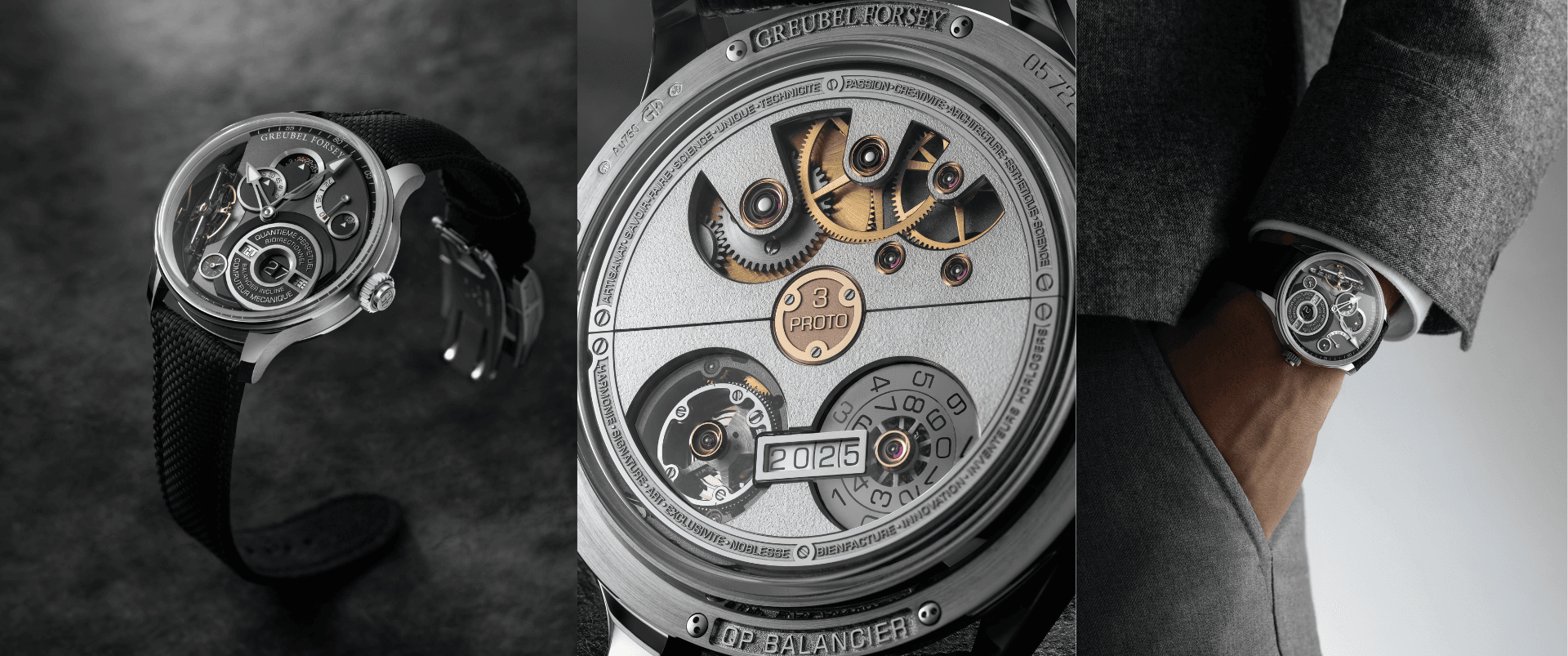
No articles found