Know Your Watches: Finishing Techniques In High-End Watchmaking - Part III
For those of you returning with an appetite for more knowledge on watch finishing techniques after enjoying the first two instalments of the latest Know Your Watches series, you’re my favorites. If you’ve missed it, don't worry, I’m not judging. (Okay, maybe a little.) Did the plot thicken without you? Fear not! Both Part-I and Part-II are still available, so catch up at your leisure! So far, we’ve covered, in alphabetic order, all the techniques from A till E. Yes, this is going to be a progression of it in a similar order.
Now, before we dive back into the regularly scheduled program on watch finishing techniques, I’m going to share a novel perspective on it. I call it the ‘decoration dilemma.’ It might be brilliant, it might be bonkers, but either way, it's a perspective you probably haven't considered.
For watch brands, many of which achieve annual production outputs of tens of thousands (some even surpass a million units like Rolex or get close to the number), there isn’t enough skilled workforce available to achieve a totally hand-finished yearly output. Also, that isn’t the objective everywhere. Yet many of these demand price premiums that make certain haute horlogerie inceptions feel like a bargain. I’m not against watches which serve bare minimum in terms of finishing, but it is the collector psyche that needs adjusting. Accepted, there’s enough matter to appreciate the level of finishing on a Rolex caliber 7140 as featured in their Perpetual 1908, the first movement of its kind intended for a sapphire caseback, hence made for decoration. But what about the Caliber SXH5 in a Czapek Antarctique. Well, you don’t need my attestation to classify one as being “window dressed” and the other as properly decorated. If you scroll through the listings on Chrono24, there’s a shocker. Between the Perpetual 1908 and the Antarctique, there’s a $10,000 disparity in favor of the former. Yes, I get it. One’s precious metal and the other steel. But $10,000? The Antarctique is a possible icon with a movement that is laboriously decorated as per the exacting standards of contemporary high-end watchmaking. It’s an in-house micro-rotor caliber with a wonderful amalgam of traditional finishing applications (plus four sharp interior angles on its mirror polished steel center wheel bridge.) The secondary market pricing is an indicator of a collector habit that’s sort of hype-contaminated and unappreciative of handworks executed on horological creations. It’s a genuine index of a corroded appetite among watch enthusiasts for artisanal movement finishing. Shame!
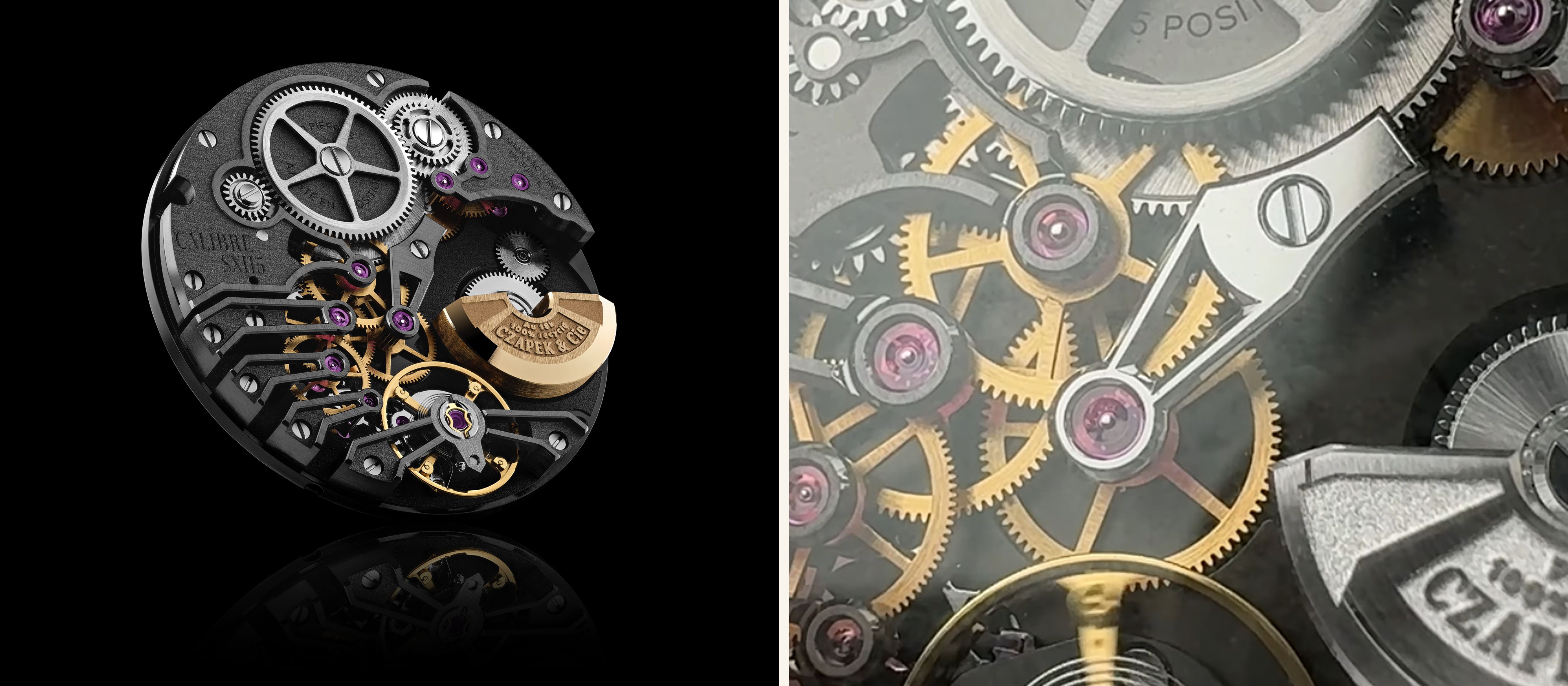
For me, ignorance isn’t a bliss. Stupidity is. That’s why I try to learn to appreciate better. This is what forms the roots to this series of which we today progress F onwards. For the latecomers, a watchmaker’s loupe can come in handy!
Frosting
Frosting is a matte finish realized on movement components such as bridges and dials through media blasting or engraving. It yields a granular patterned surface by carving or directing a highly pressurized stream of sand or beads resulting in fine indents on the surface, thus avoiding any material removal. Horological frosting is achieved through the techniques of “Tremblage” or “Grenaillage.” The former technique is realized by burin-engraving the surface by hand through a series of uniform pin prick marks. It can also be achieved by a hammer and chisel. The latter technique of grenaillage involves projecting tiny abrasive grains at a surface to give it a rugged granular texture. Apart from yielding a matte finish surface decoration, it helps with corrosion resistance to some degree.
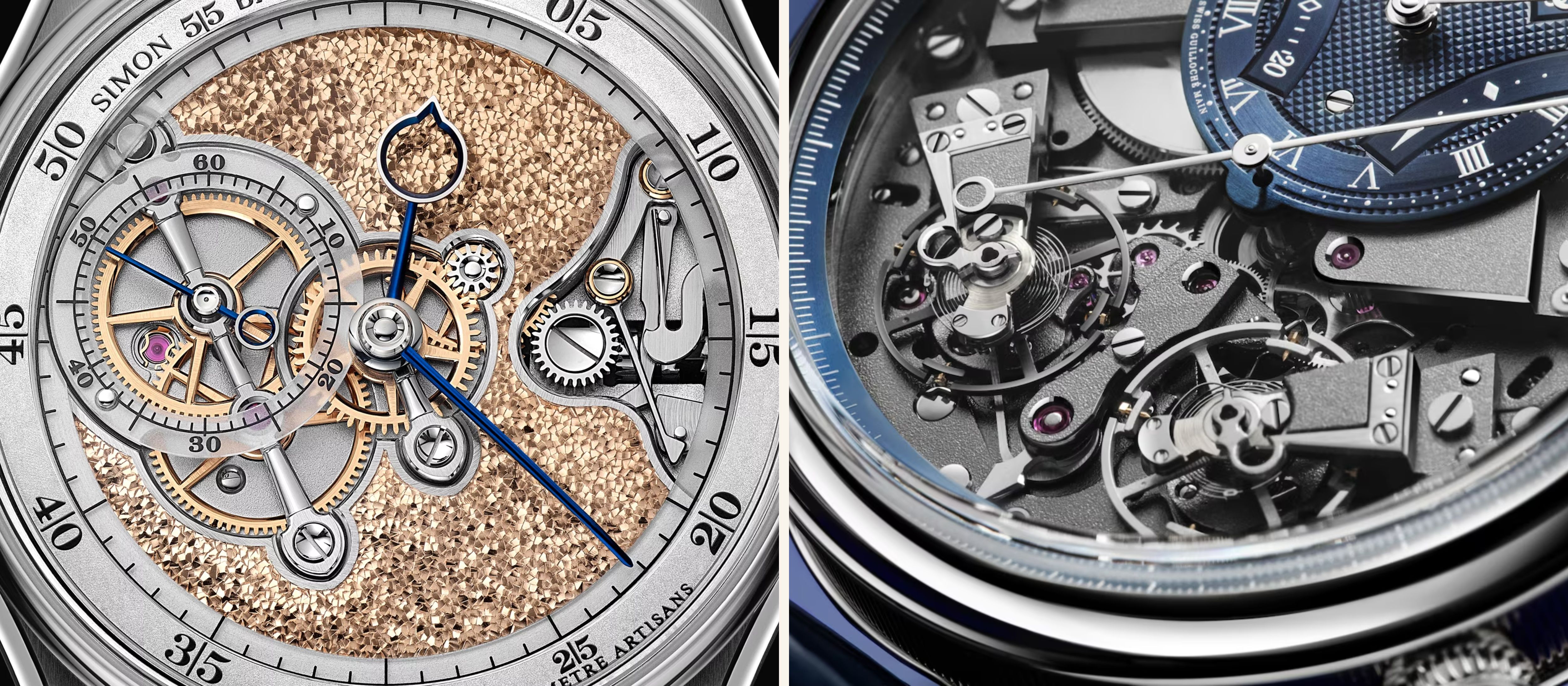
Gratté-boisé
The finishing technique of gratté-boisé is a modified engraving process realized through scraping of a surface by hand, usually with a wooden tool that resembles a scraper. It is a time-consuming process requiring alternating between scraping and polishing. Its benchmark execution is the German silver base plate on the Greubel Forsey Hand Made 1 Tourbillon.
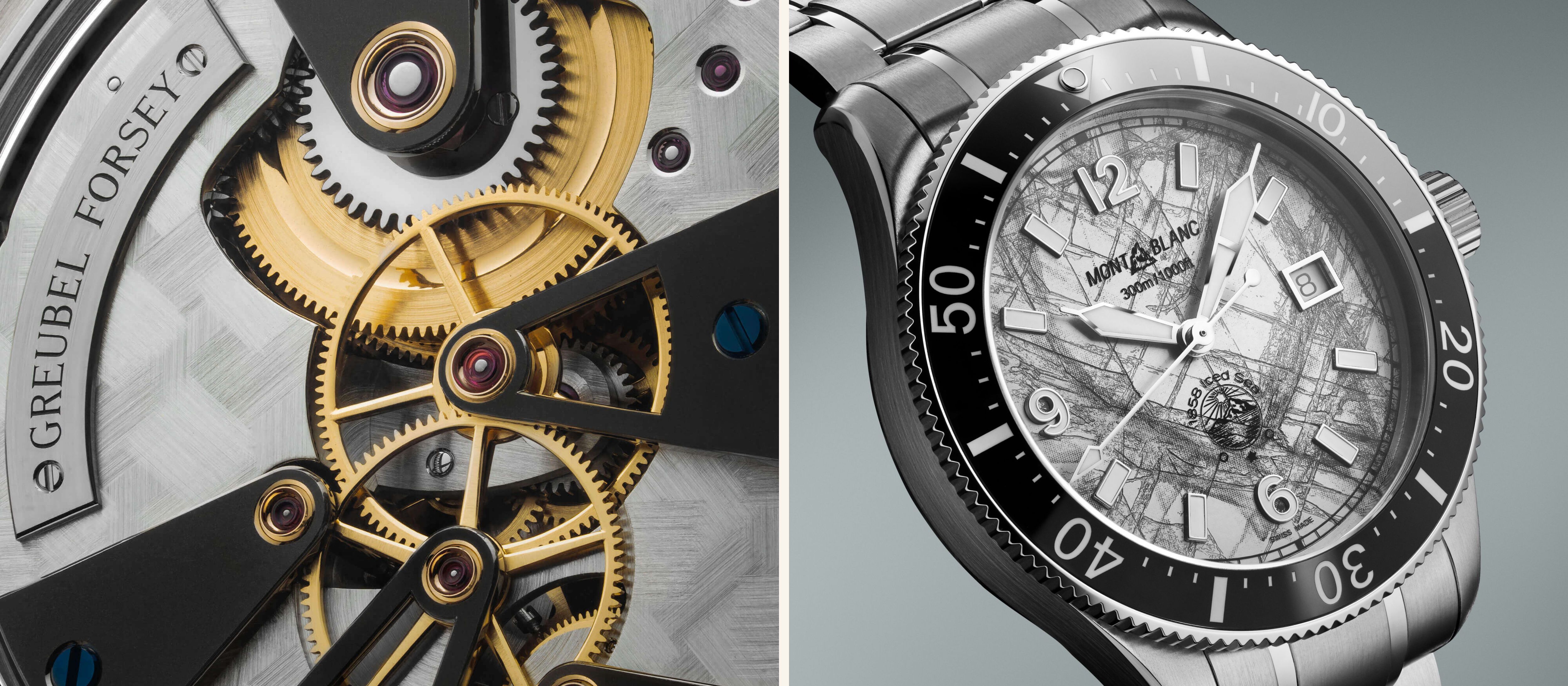
Guilloché
Guilloché is a traditional mechanical engraving technique that involves carving intricate geometric patterns on a metal surface for aesthetic gains as well as better legibility. It is one of the most visible decorative artforms that adorn watches. The creations of Abraham-Louis Breguet are the inceptive horological works featuring this decoration technique as it was introduced by him in watchmaking in around 1786. In contemporary watchmaking, guilloché is used to decorate watch dials, watch cases, oscillating weights and even movement components like bridges.
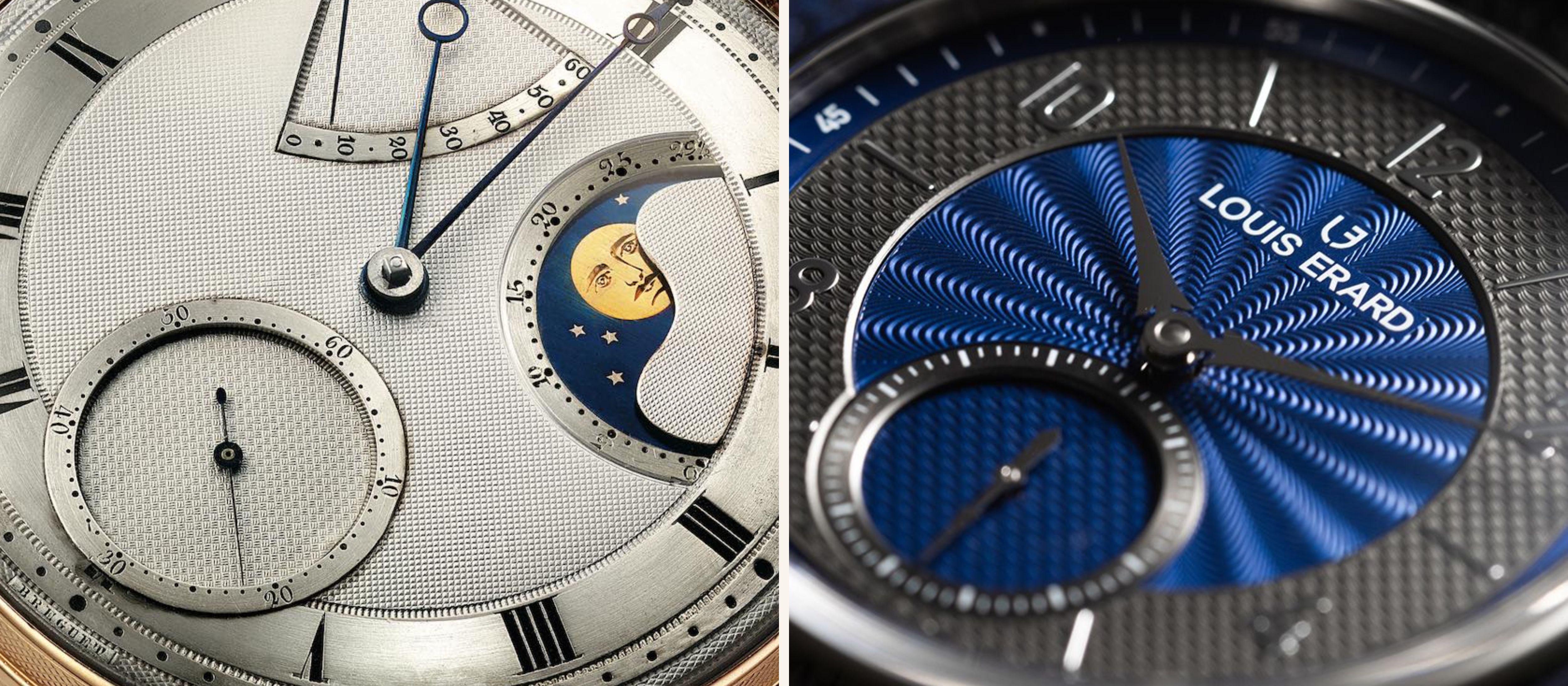
Traditional hand-guilloché is a completely manual process realized through engine turning on a straight-line engine lathe also known as a rose engine machine. It’s a very rare and specialized craft demanding higher skill levels. A pre-programmed wheel called a rosette, makes cutting a precise and consistent pattern on the metal surface possible. A straight-line engine works on the same principle but allows for a linear cut. Modern demands of guilloché have led to an industrialization of the technique which can be realized through a CNC machine or even by stamping the surface. While these methods are inexpensive and better suited for larger production volumes, a hand-crafted guilloché surface offers a distinctive lustre and is revered by purists. There are different kinds of guilloché based upon the types of established patterns carved on the metal surface. These include:
Clous de Paris or Hobnail: This is the most commonly used guilloché technique executed on a straight-line engine lathe. It is achieved by cutting hollow intersecting lines along the surface which results in formation of tiny pyramidal shapes. This relief which lends depth to a surface can be found on watch cases and dials.
Barleycorn or Grain d’orge: A barleycorn pattern is a vertical or radial arrangement that involves cutting parallel or concentric wave-like lines into the metal surface. Also known as Grain d’orge, this guilloché technique results in a fantastic visual effect resembling tiny eye-shaped patterns across the surface. This pattern is executed using a rose engine machine.
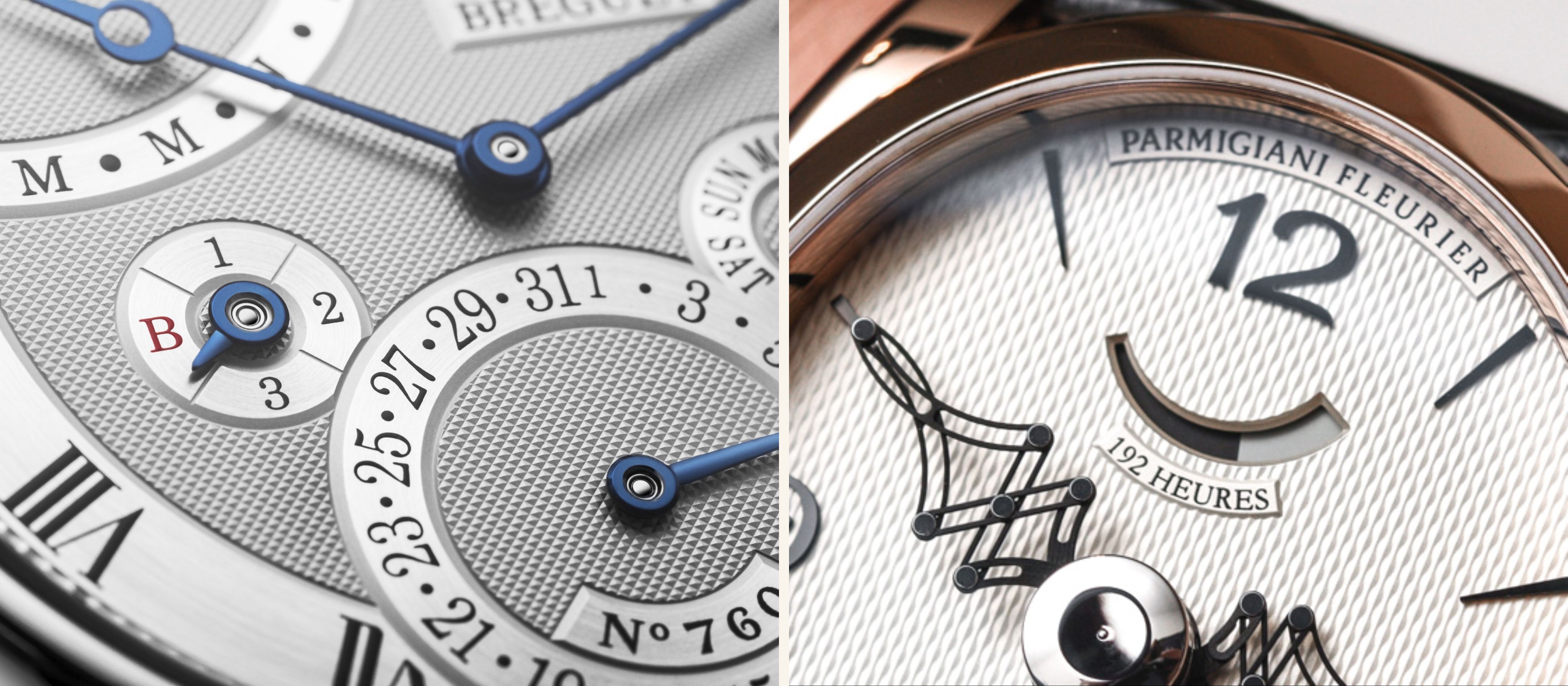
Sunburst: This technique involves carving finely-engraved lines radiating outwards from the center of the dial. Executed on a straight-line engine, the technique, although comparatively easy to execute, yields an aesthetic with depth.
Tapisserie: This is the type of guilloché found on the dial of an Audemars Piguet Royal Oak and that’s enough to explain its flat-topped square patterns on the dial surface. A modified Clous de Paris technique, Tapisserie occurs in different types depending upon the sizes of the repeated squares. It is crafted on a straight-line engine.
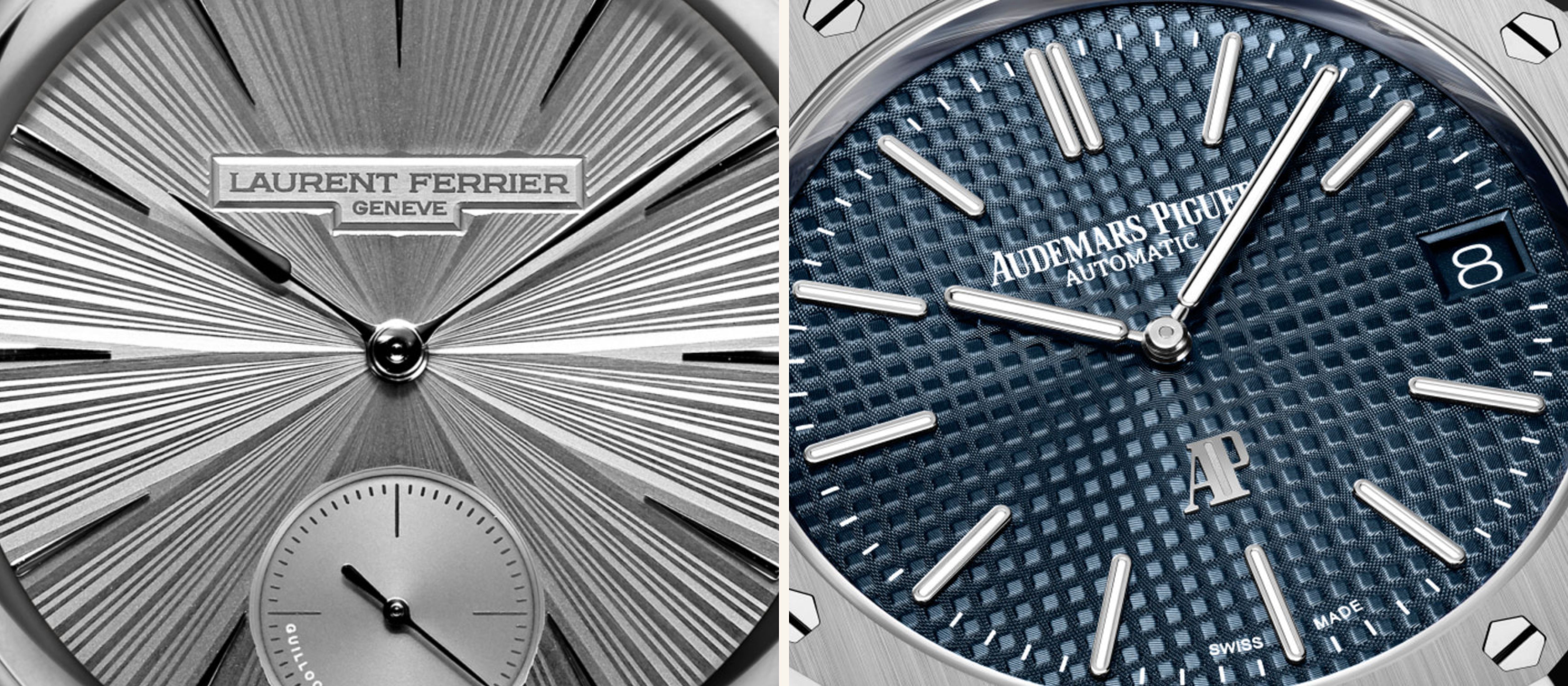
Basketweave: This guilloché technique is very traditional to English watchmaking and one of the most difficult ones to execute. Resembling a basketweave pattern, this technique involves alternative repetitive advances to be made in order to leave spaces to be guillochéd later in the perpendicular direction to create a weave-like pattern. It is also performed on a straight-line engine.
Others: There occur other guilloché types which are sort of modified traditional patterns such as the Flinqué or waves pattern, Écailles de poisson or fish scales guilloché, Moiré and Grain de riz. Some techniques are singular to the watchmakers and are also modified adaptations such as the ‘Ricochet’ guilloché on Czapek dials and the ‘Infinity’ wave on J.N Shapiro watches.
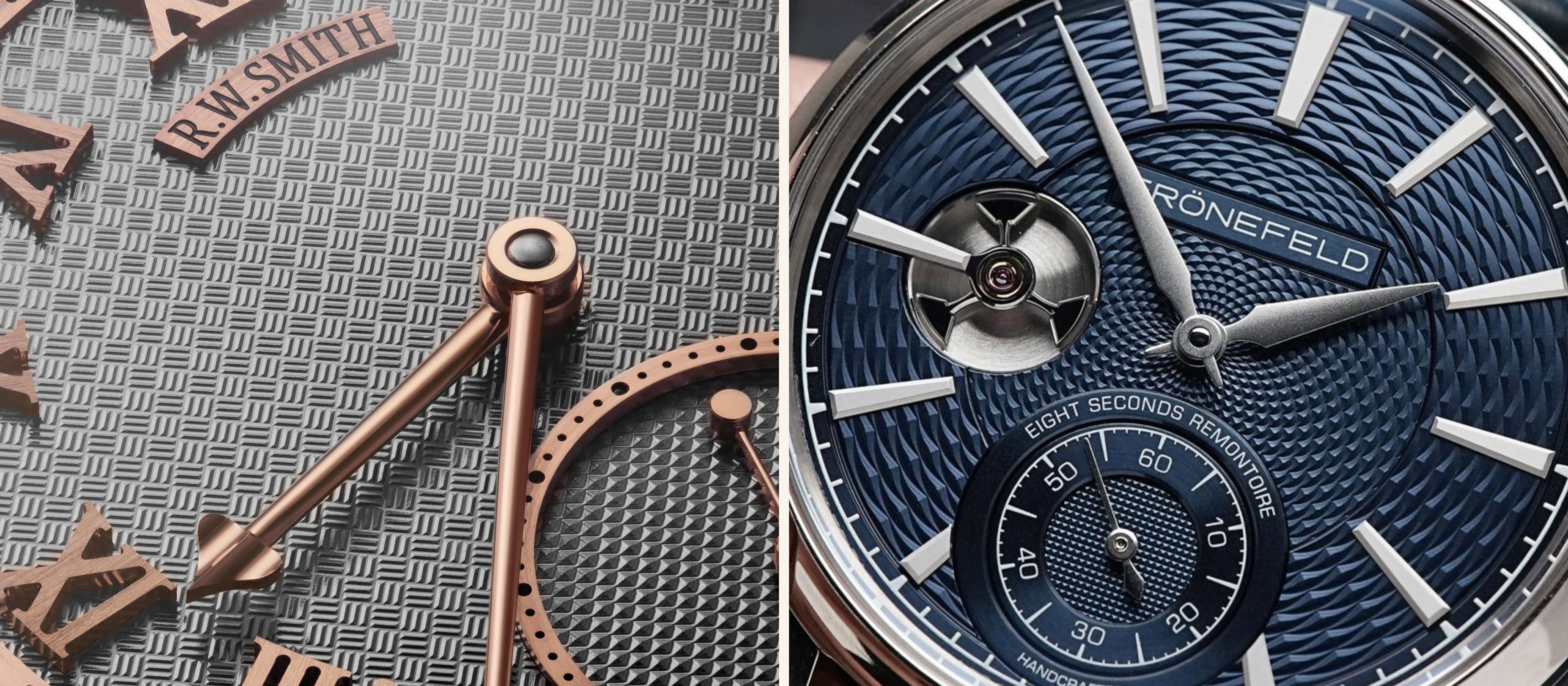
Perlage
Perlage, also known as circular graining or stippling, involves creating a pattern of overlapping small circles on the metal surface. It is executed by a rotating peg and is often applied to hidden surfaces on a watch movement such as the back surface of the mainplate or even the underside of a caseback. In some instances, high-quality perlage is applied to decorate the dial components on an open-worked watch. Apart from its decorative intent, perlage is performed to ensure adhesion of small metal particles or chips that are formed over time due to abrasion between moving components. The main complexity in realizing a flawless perlage is usually the consistency and uniformity in achieving the effect.
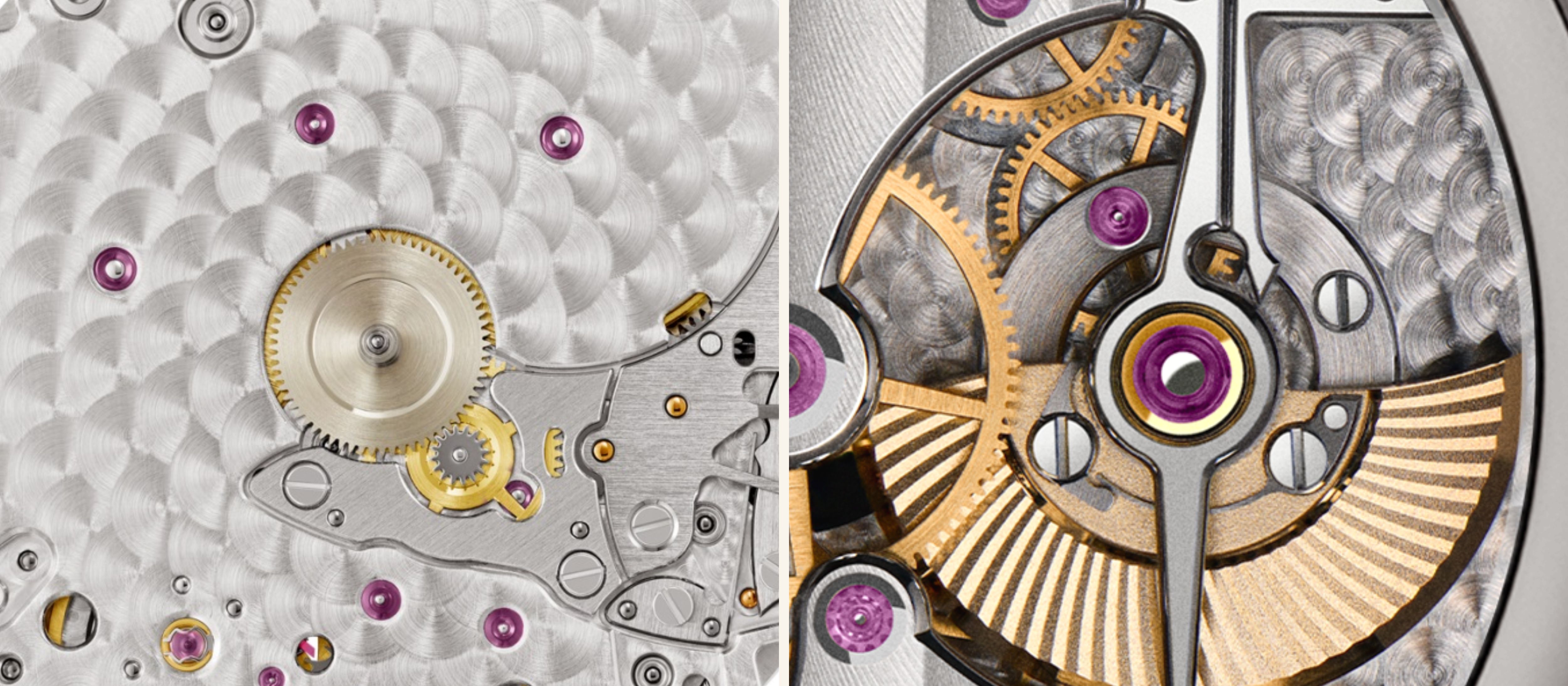
There’s joy in small things and absolute ecstasy in the detail of those small things. When you observe watches very closely, you unearth an inward universe of micro-mechanic finesse that, much like the inward universe within us, carries the true spirit of the creator. It not only takes a loupe but a simple yet uncommon thing we call “attention,” not merely as a passive observation but as an active engagement, to cultivate a quiet reverence for the artistry, the patience and the ingenuity that realizes such miniature marvels. It is in this attentive perception of the small, that we discover the profound.
We’re almost on the final leg of our watch finishing exploration. In the last part of this Know Your Watches series that’ll soon follow, we’ll cover the remaining techniques and find some more matter to make your eye loupe shopping every bit worth it.
No articles found