Know Your Watches: Finishing Techniques In High-End Watchmaking - Part II
When you’ve seen enough watches, it’s possible to institute a definitive line of differentiation that separates the concluding realizations of the watchmaking craft. In every timepiece you observe, a critique can be understood and established of the cumulative labor demanded by each and there’s levels to it. High grade fine watchmaking is the 21st century realization of anything and everything that demands museum-worthy curation in the ages yet to arrive. And its finest artisanal sentiment lies in finishing or decoration. Of the many crafts we associate with luxury watchmaking, this is fundamental in yielding an object of higher artisanal value. Occurring in an almost infinite price-based assortment, wristwatches of the modern-age aren’t all alike. In the leading instalment of our latest Know Your Watches series on “Finishing techniques in high-end watchmaking,” we sort of established the markings of differentiation as to why a luxury watch can cost anywhere from $500 to anywhere in the range of a $100,000 and all answers lie in the discipline of finishing and its approach as well as levels of execution by the respective luxury watchmakers.
This second part of the series builds upon the already-established alphabetic indexing of watch finishing techniques with some lumens focused on the challenges and touchstone executions of each. Here’s to add to your workout with the eye loupe. You got one, right?
Brushing
Brushing serves as a broad classification for a multitude of watch finishing methods. It is actually a very simple process and so commonly observed in watchmaking that it gets relegated as not a real decoration. However, like with any other finishing technique, there occur levels to it. In its essence, brushing or satination is a treatment involving marking the surface with a fine etched non-reflective linear, radial, circular or snailing pattern.
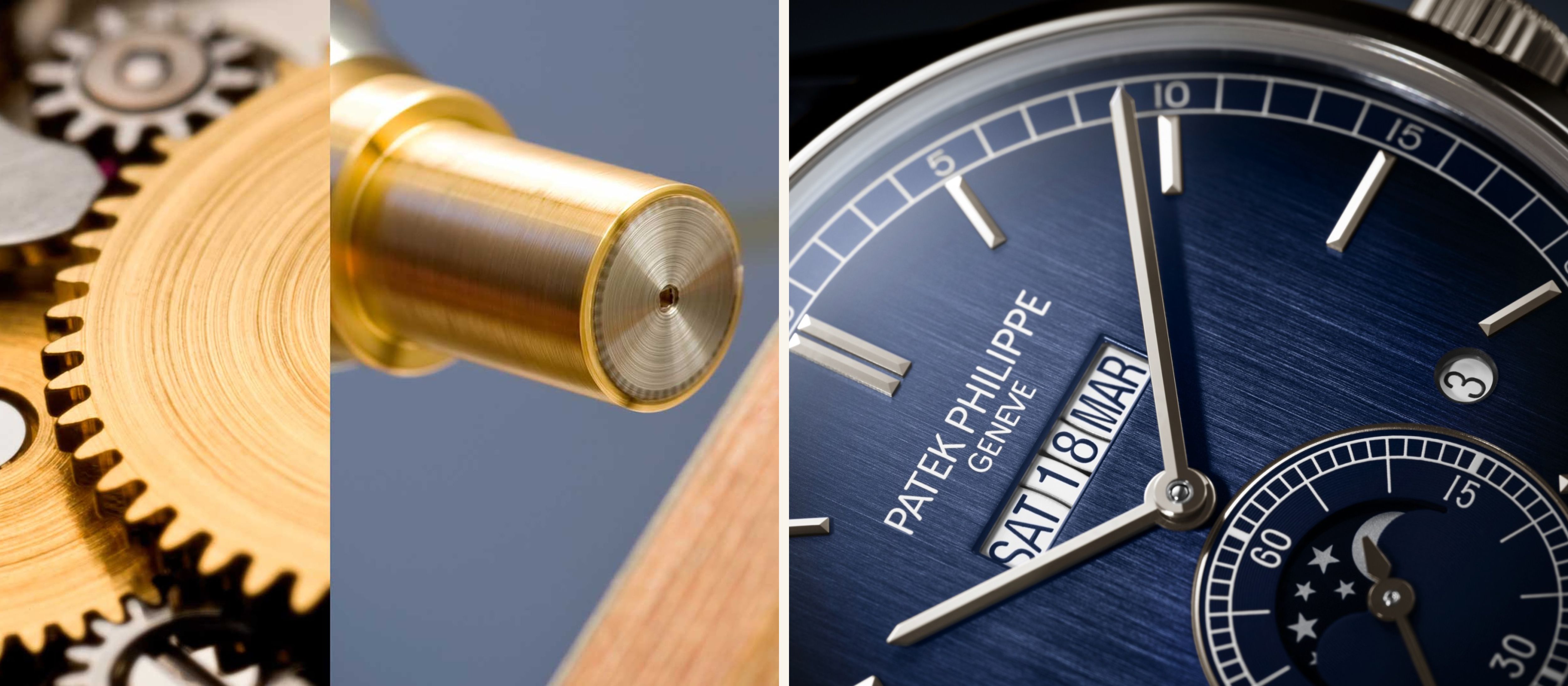
Among the many types of brushing include circular graining performed on watch wheels with non-overlapping concentric circles radiating outwards. Snailing or soleil, sometimes referred to as colimaçonnage or solarization, involves etching curved outward radiating lines from the center. A more complex execution of snailing is double-snailing where an inner and outer ring of snailed finishing is observed but with opposite direction of the curves. It’s usually performed on large wheels. In sunburst finish, which is most common on watch dials, a sunray-like pattern emanating from the surface is etched. Linear satination or vertical brushing is another technique commonly applied on watch dials, movement bridges, cases and bracelet components.
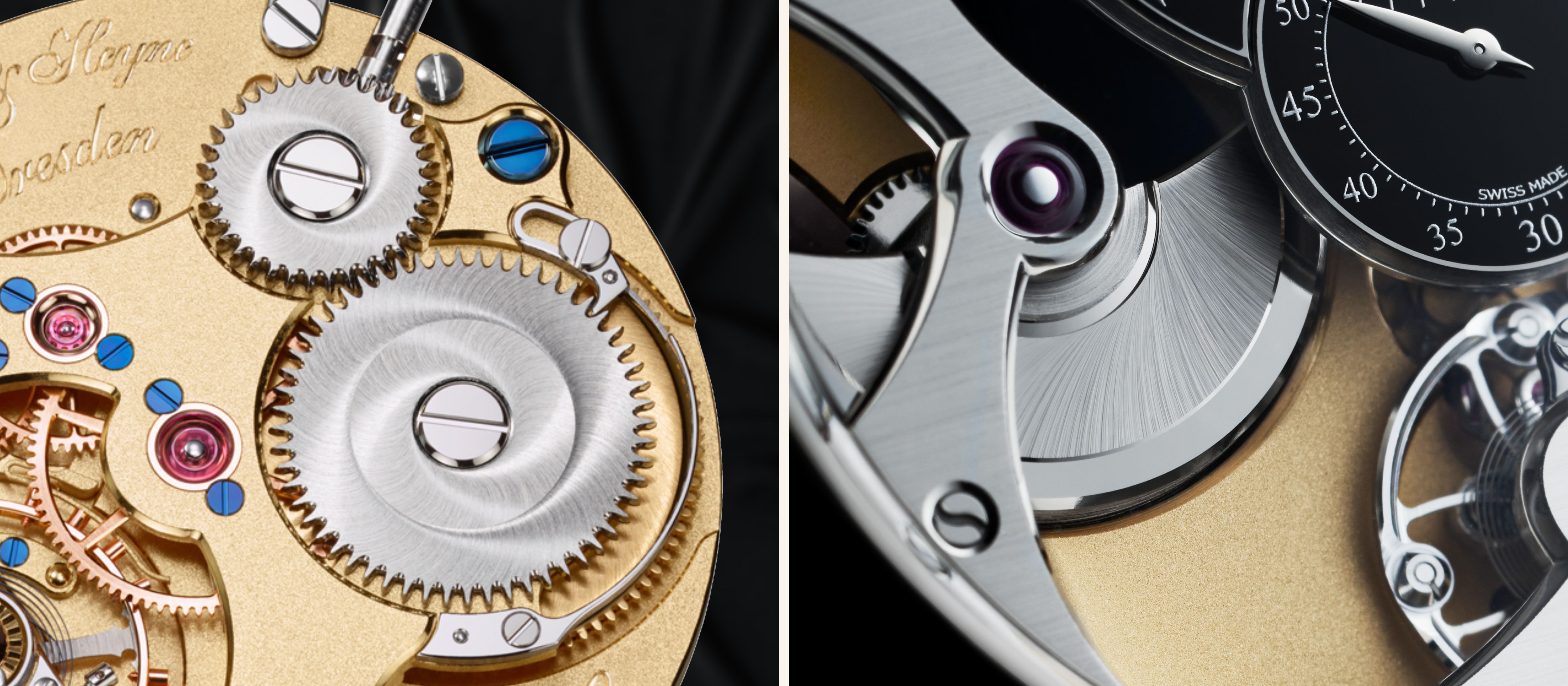
Take a look at the double snailing on the ratchet and crown wheels of Caliber VI on Lang & Heyne’s Friedrich III. It is a hypnotizingly complex aesthetic from a simple technique. The colimaçonnage on Romain Gauthier timepieces is exceptional with snailing performed as fine brushstrokes.
Engraving
Engraving, notably hand-engraving, is a finishing technique that finds its roots in jewelry making and when embellishment of watch cases and movements became a thing, the technique soon found perpetual employment in horological crafts. In regards to watchmaking, this technique is practiced in two ways - chasing and engraving. While both are same, chasing involves pushing the material so as to carve a relieved or raised pattern by creating ridges that make up the desired shape. Engraving is the process of removal of material from areas that form the desired shape. There occur a multitude of iterations and styles to both and the end result catches the light differently than its surroundings to add unique brilliance to a watch movement or a case. Notable executions of hand-engraving include the hand engraved motif on A. Lange & Söhne balance cocks. The Patek Philippe 6002R features an ornate execution of chasing on its precious metal case.
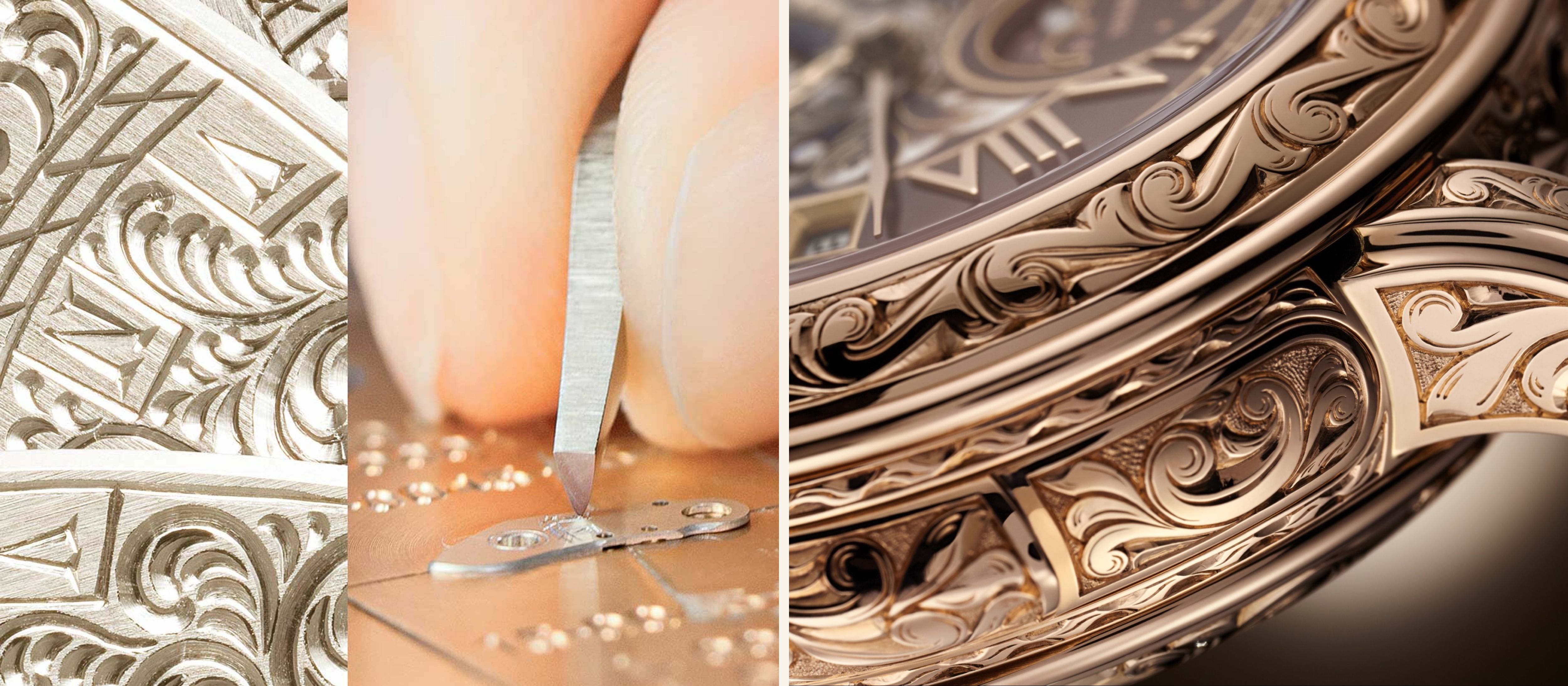
Enameling
Despite its widespread recognition, enameling is a skill that only a few possess and even fewer have mastered. Moreover, its rarity makes it a prestigious decorative technique dominantly used to adorn watch dials and even casebacks. Enamel is composed of silica or transparent glass which in combination with a variety of other elements can be fired to melt and fuse with the base metal in the desired artform or pattern. Garnishing the horological crafts, there occur a number of different effects of enamel works each achieved through a different technique as explained under.
Grand Feu: Translating to “great fire,” Grand Feu is the most common horological enameling technique in practice. Achieved by layering enamel, this repetitive process involves subsequent firing in a kiln after each enamel application at a minimum of 700°C. The result is a hard but brittle non-fading surface. The technique though common is by no means easy with a high failure rate resulting in only 40% success probability.
Champlevé: This enameling decoration is realized by filling petite cavities or hollows directly on the dial with moist powdered enamel which is then fired and repeated until the final layer is achieved. A subtle hint of the metallic edge around the grooves is left in order to create a separation between the base metal and the enamel itself. Any excess enamel can be removed by soft sanding.
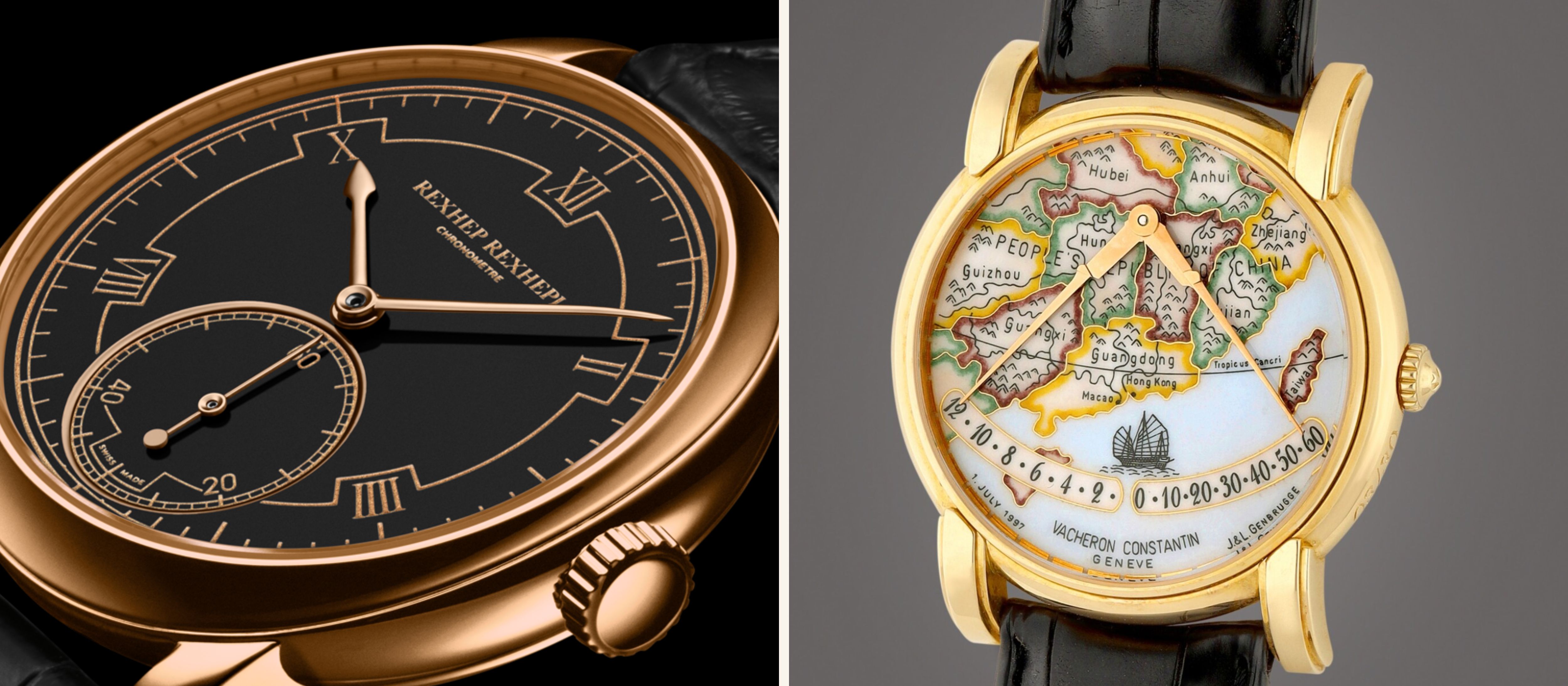
Cloisonné: This technique is Champlevé’s synonym in approach but counterpart in execution. In cloisonné enameling, a thin metal wire is used as a parting surface to create the desired motif which can subsequently be filled in with colored enamel. The cloisonné technique allows for higher intricacy in details and designs with better color separations made possible. The wire which is usually of a precious metal material forms a fence that yields the final pattern and is even visible in the end-result. This technique too requires multiple layers of enamel to be applied and fired.
Flinqué: The technique involves covering any guilloché or engraving on the dial with enamel layers acting as a protective as well as decorative coating for the motif. Like the techniques above, flinqué too requires multiple layers of enamel application and subsequent firing. The end result is a translucent enamel layer that shows the beautifully intricate guilloche pattern beneath.
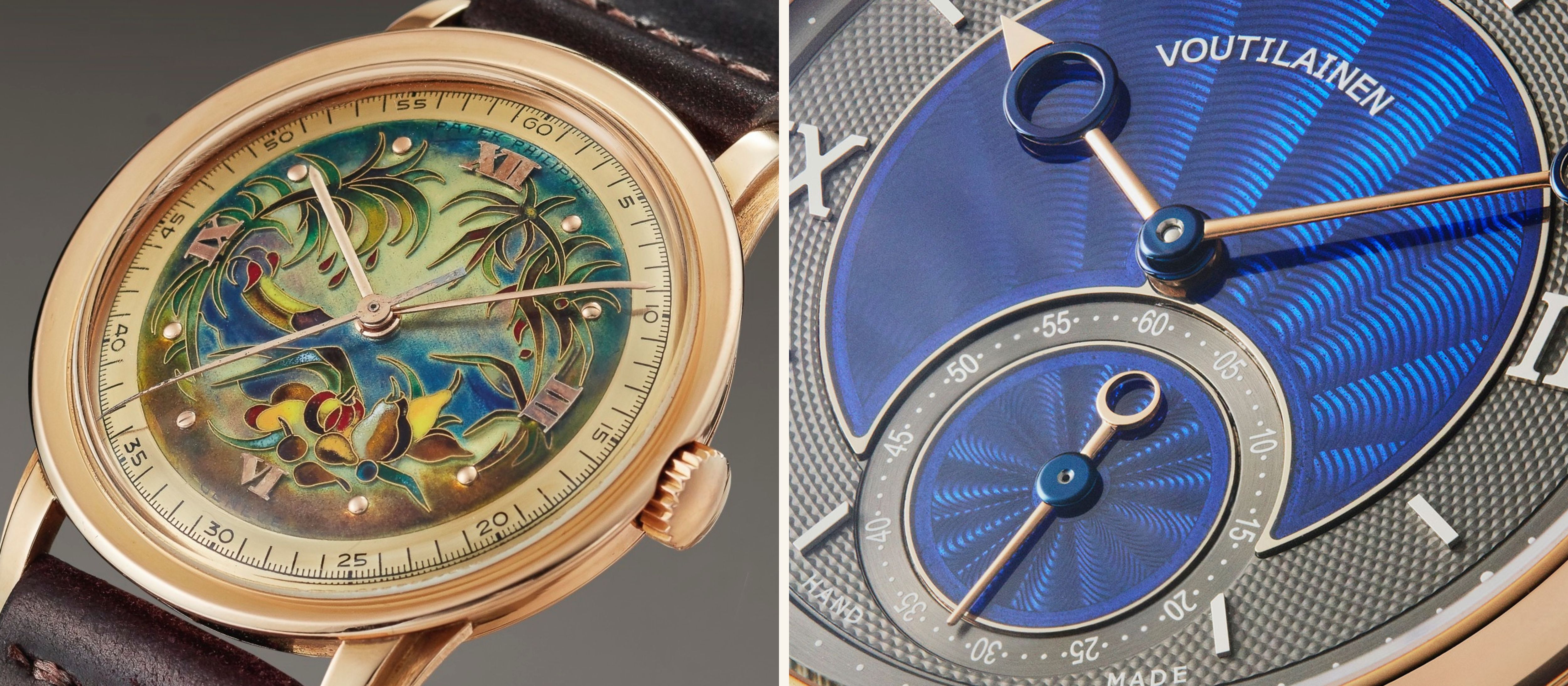
Plique-à-jour: This technique is equivalent to an evolution on cloisonné but without any base metal backing required. The patterns and partitions created by thin metal wired are occupied by enamel and without any metal base in place, the result is a translucent suspended enamel surface allowing light to pass through it. The temporary backing used during the technique is carefully removed by rubbing or acid dissolution making the process highly prone to failure.
Paillonné: This is a two-part technique with the first process resembling a flinqué technique with subsequent positioning of paillon or thin foil pieces sealed with translucent enamel layers imparting a translucent depth to the dial.
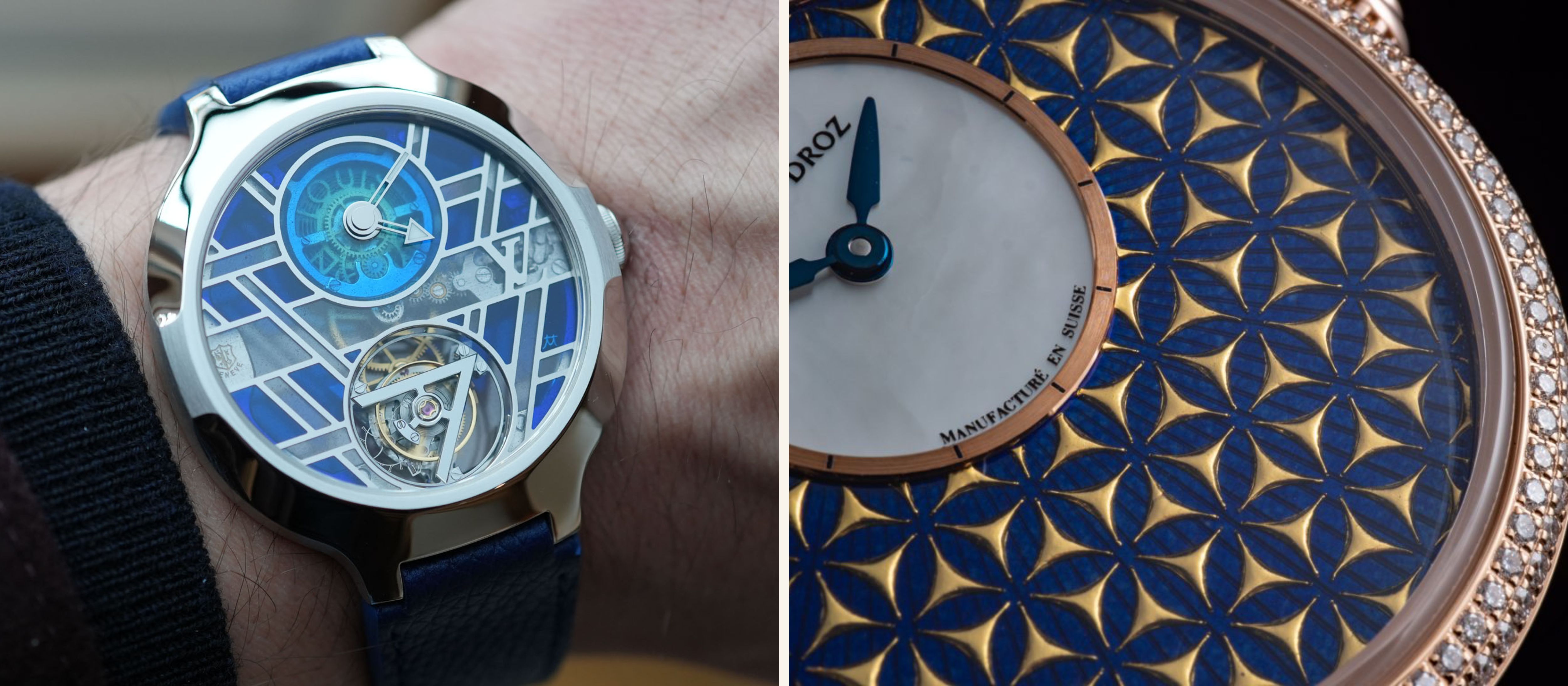
Grisaille: The concept behind grisaille is to impart realistic effects to enamel by using lights and shadows. It is based on the “chiaroscuro” effect from light-dark colors. The base metal is coated with a black or dark blue enamel layer on which a light or white paint known as “Blanc de Limoges” is applied in varying thicknesses. This two-tone effect creates a three-dimensional surface motif usually realized in monochromatic hues.
Miniature paintings: This is very suggestive as the technique relies on creating intricate hand paintings on a base already enameled with grand feu. Subsequent colors are added layer by layer without partitions resulting in a very singular petite artwork devoid of any partitioning lines. The technique is prone to failure during final firing that can cause hairline cracks on the enamel layer thus demanding absolute mastery in execution.
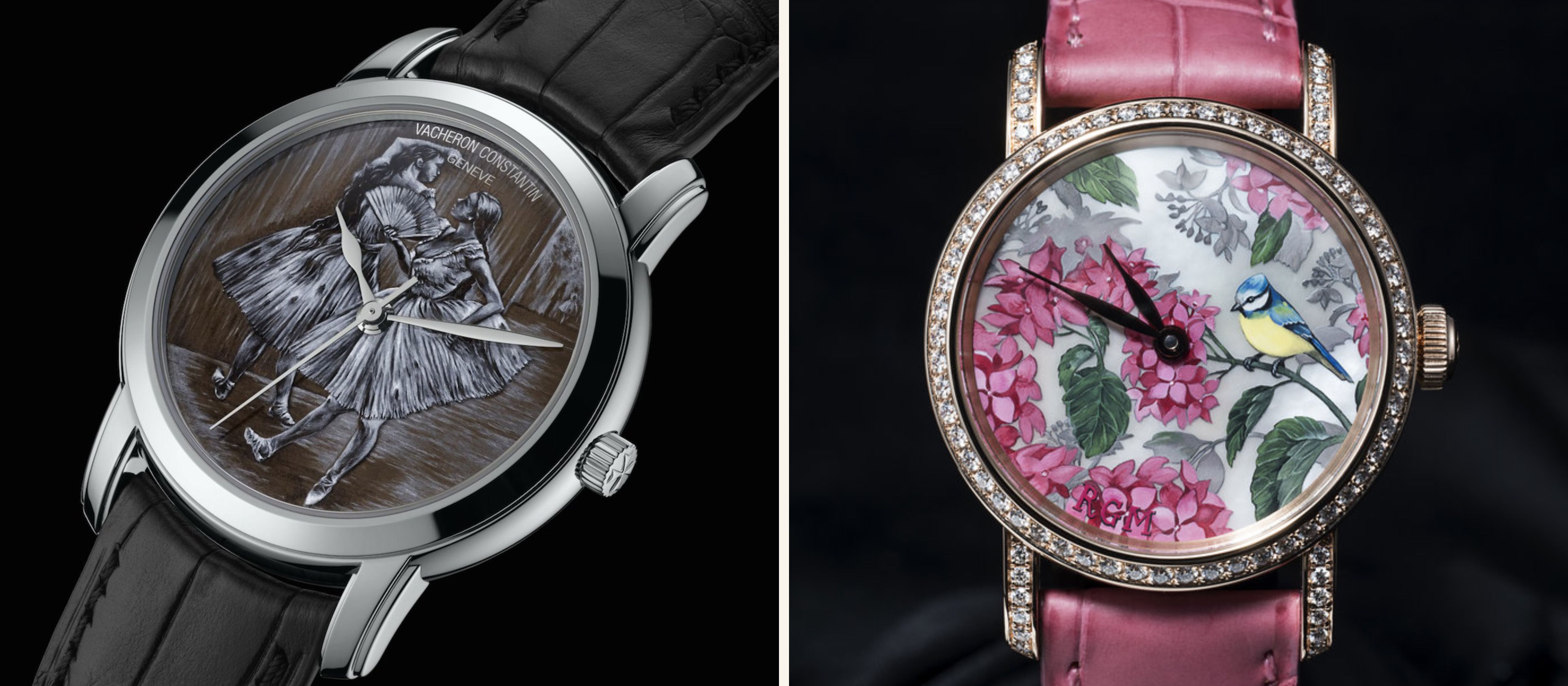
Modern high-grade watchmaking is a spectator sport of sorts with a strong competition brewing in perfecting the levels of finishing achieved on the many petite components making up a fine timepiece. It takes patience and an artistic perception to fully understand as well as savor the intricacy of crafts going into perfecting these tiny machines. For now, test your loupe to the max with what you’ve learned and keep it spot-free for the next instalment of our Know Your Watches series on watch finishing.
No articles found