Know Your Watches: Finishing Techniques In High-End Watchmaking - Part IV
“Quality means doing it right when no one is looking.” These words of Henry Ford establish a formulative standard in higher executions across broader disciplines. Occurring as a 21st century fundamental anomaly, mechanical watchmaking actually doesn’t entail an imperative utilitarian relevance in the “smart age.” Yet, we find its apex realizations permeating the quality sentiment and objective to not only acts beyond surveillance but even across aspects in veil. Had Mr. Ford been a maker of watches and not automobiles, he would very much have believed: Quality means doing it right where no one is looking. This variance from when to where is what has been the subject of focus in our latest Know Your Watches series, of which we’ve already sculpted a threefold analysis. The soul of watchmaking quality resides in the levels of finishing executed on the many petite components making a timepiece. It is a differentiator of major sorts and the chief attribute emphasizing the fine realization of the watchmaking craft.
Throughout Parts I, II and III of our exploration of watch finishing/decoration techniques, we’ve alphabetically covered the techniques from A till P. We’ve ventured deep into the processes, challenges as well as benchmark executions of each. By the end of this article, you'll be able to spot perlage from a meter away and explain anglage like you invented it. Moreover, you’ll find yourself appreciating watches and watchmaking with a confident stance. Like the next time you get a chance to go hands-on with a Glashütte Original PanoReserve, you’ll find yourself murmuring, “Hmm, not bad.”
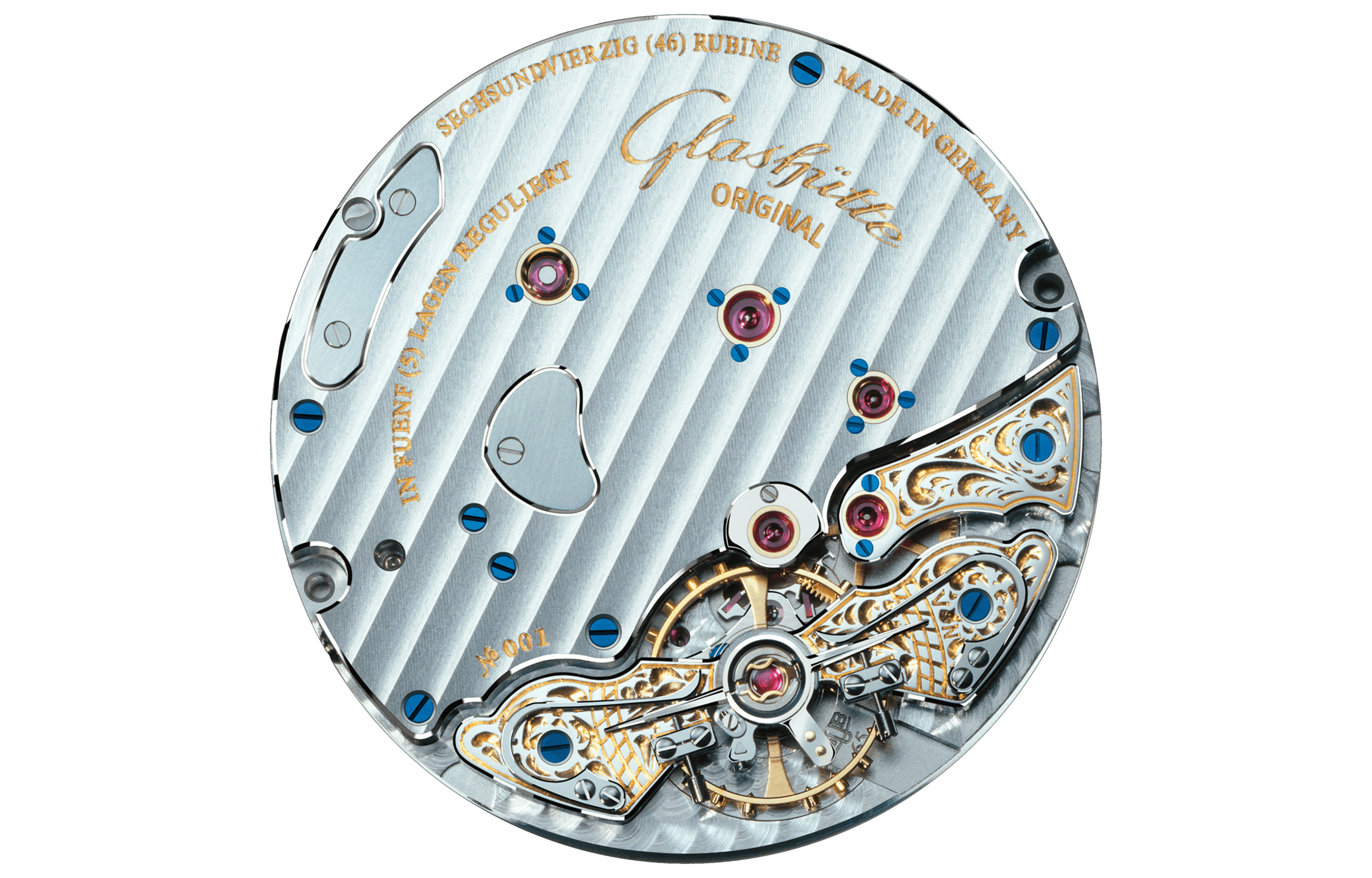
So, wipe your watchmaker’s loupe clean for we’ll get on with our regularly scheduled program. This time we’ll find a conclusion to the series as we’ll have covered the many finishing techniques specific to watchmaking, all the way from A till the alphabetically last decoration. Let’s start with the remainders of “P” from the previous instalment.
Plating
The only credible attribute legitimizing plating as a watch finishing or decoration technique is the visual alteration it renders on a watch component. Unlike any of the crafts we’ve studied till now, this one is more of an alchemist’s endeavor. Brass usually serves as the base material for watch movement bridges and plates. To elevate the aesthetic finesse of this humble metal, various plating techniques are employed. Gold, nickel, and rhodium plating are commonly utilized, offering the visual characteristics of precious metals while providing a cost-effective solution. It is an economical replication of the precious metal finish. Many vintage calibers from Omega feature a distinct reddish hue resulting from copper plating. The strategic application of plating on watch calibers and even dials also renders functional benefits in regards to better corrosion resistance. However, a refined aesthetic impact is the prime objective.
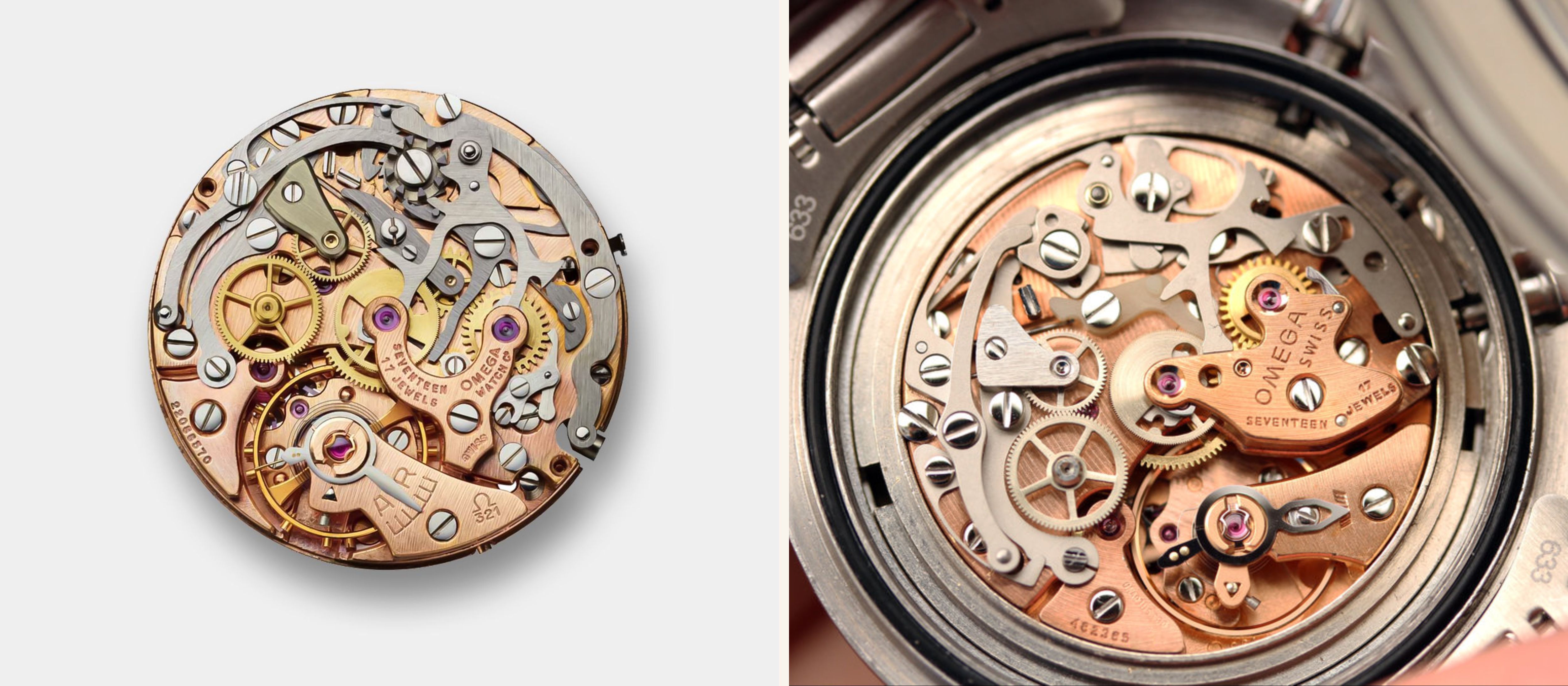
Polishing
A video titled “Pinion Flank Polishing” has 152,727 views on YouTube. It shows a watchmaker applying polishing to a pinion flank in the traditional way. The detail, labor and expertise are irrefutably evident throughout the 4 minutes and 51 seconds demonstrating the procedure. While it might look impossibly complicated to realize perfectly, the watchmaker, Roger W. Smith, is more than competent in excelling the outcomes. Irrespective of the fine surface yield, polishing generally is a progressively inverse abrasive process making surface imperfections smaller and smaller until almost invisible. The progression in abrasive diamond pastes ranges somewhere from 400-grit to anywhere in the region of 20,000-grit to achieve a flawless black-polished surface. It is usually performed on a pewter plate via a linear, circular or figure-of-eight rubbing motion. Achieving such an unblemished surface is a task reserved for only the best in the discipline and the protagonist in the video demonstration of above is certainly a master in this trade.
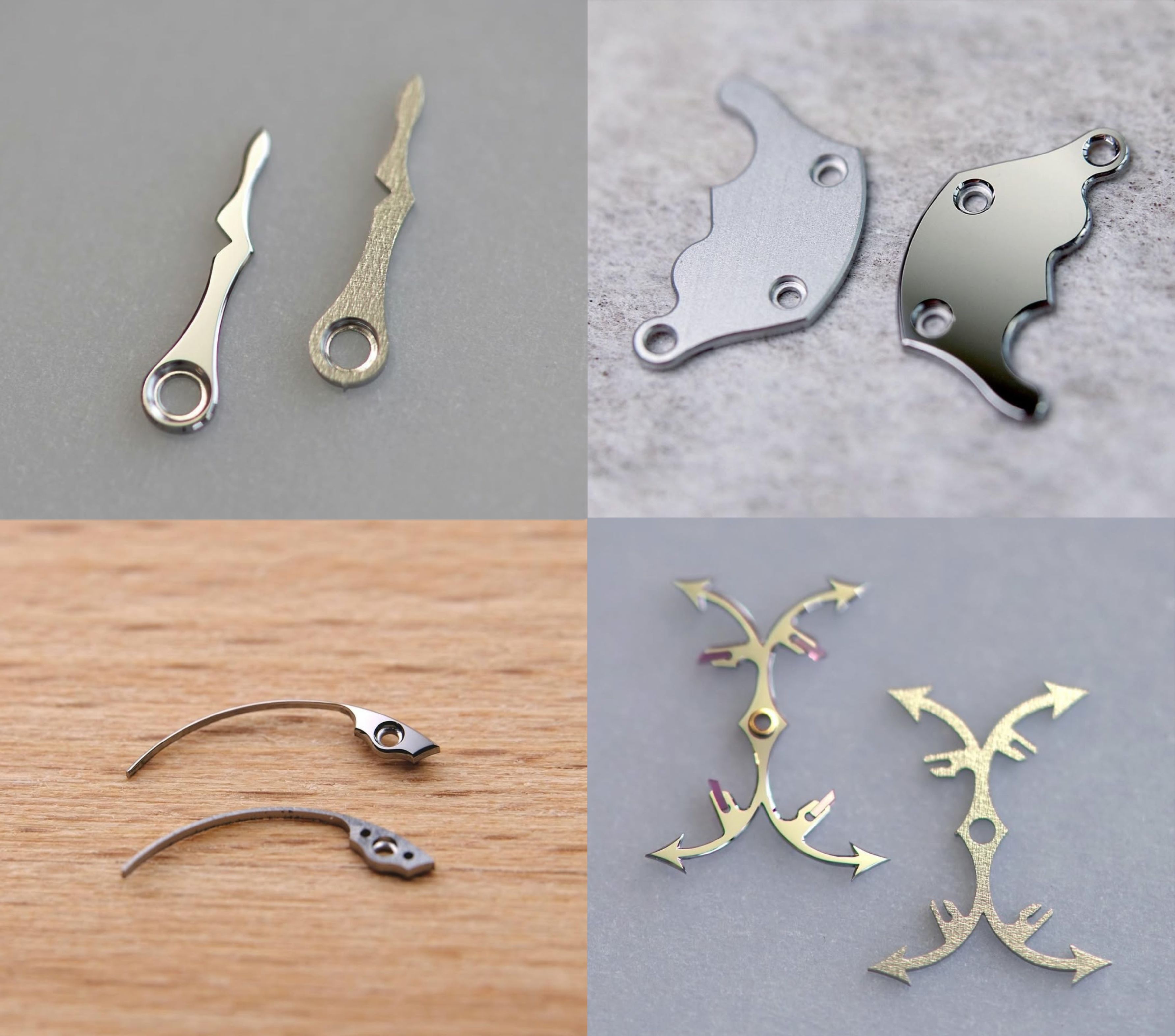
Characterized by its intricate nature and considerable time investment, this particular finishing method stands as one of the most demanding. It’s only performed on steel surfaces. Polishing or black polishing produces a remarkable reflectivity which yields a captivating visual effect, rendering the surface seemingly black when observed from specific angles. Hence, the name black polishing. This exacting finish is frequently applied to movement screws and may also adorn bridges or other components. As the process relies on removing any surface scratches, imperfections or blemishes, black polishing can risk making even the tiniest scratch easily visible. Gradual perfection of the surface makes any imperfection invisible thus elevating the process complexity even further. To remove all scratches, by all I mean literally not even a microscopic blemish shall persist, it takes time and experience, and that too lots of it. Helping reduce the risks of oxidation, black polishing coms with functional benefits as well.
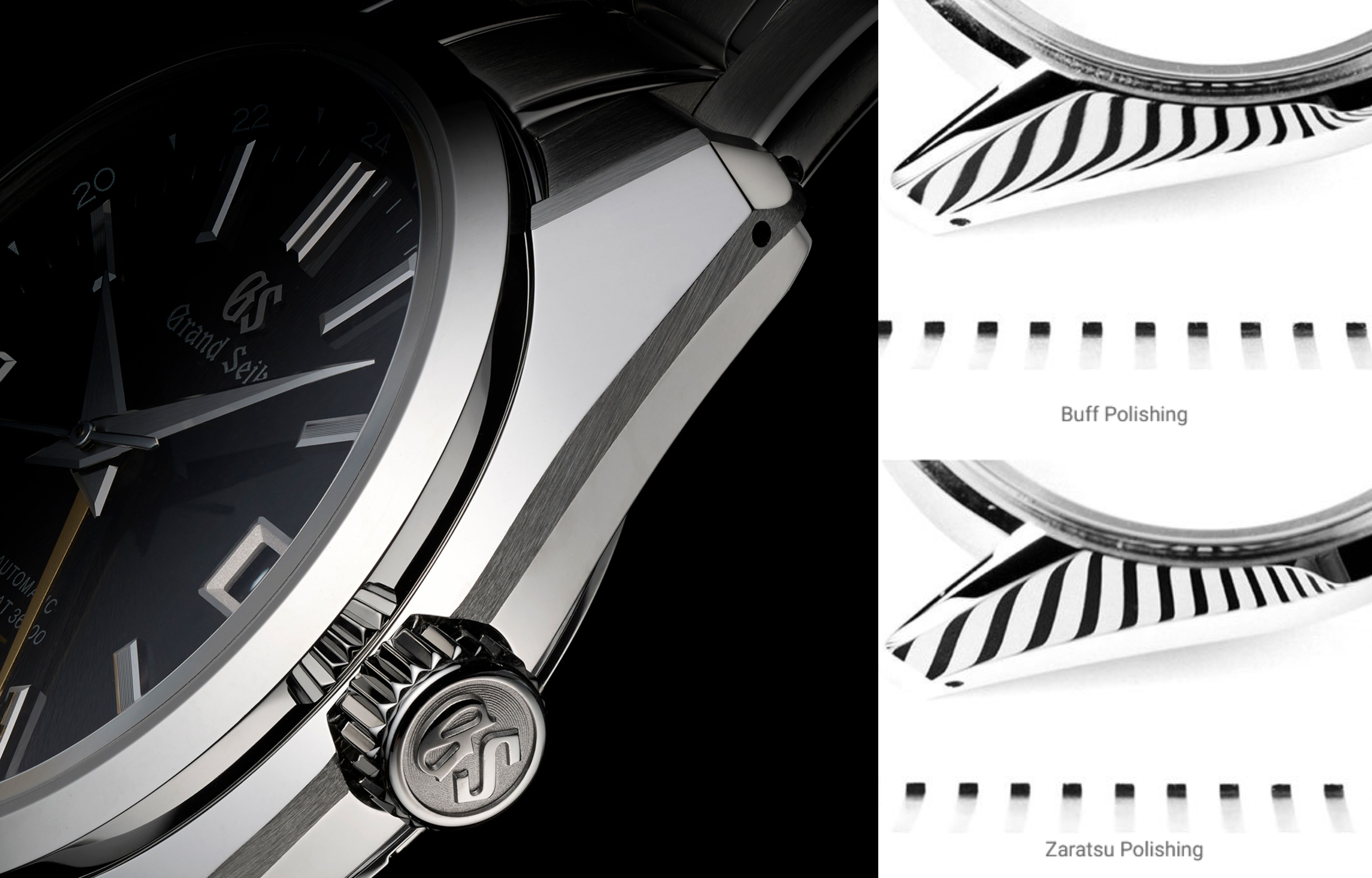
A regionally popular execution of black polishing is the Zaratsu polishing technique. Although not exclusive to Grand Seiko, which has become a lead purveyor of its broader executions, Zaratsu polishing results in creating a flat, distortion-free and mirrored surface. It is usually applied on all flat surfaces on Grand Seiko cases and hands. This technique stands as an industrial derivative of traditional black polishing and thus can be economically executed at scale. Like traditional polishing, the technique is largely based on intuitive feeling and thus perfection only comes with time and experience.
Sinks
Sinks are the concave chamfers around screw heads and even jewels. They are carved by a rotating tool and polished to a mirror finish. These screw holes within plates and bridges are machined, followed by hand-polishing that incorporates a subtle anglage or chamfer along the hole's edge. This creates a countersink, enabling the screws to sit flush against adjacent surfaces. Polished sinks also feature in the screwed chatons which usually serve as bushings for the bearing jewels.
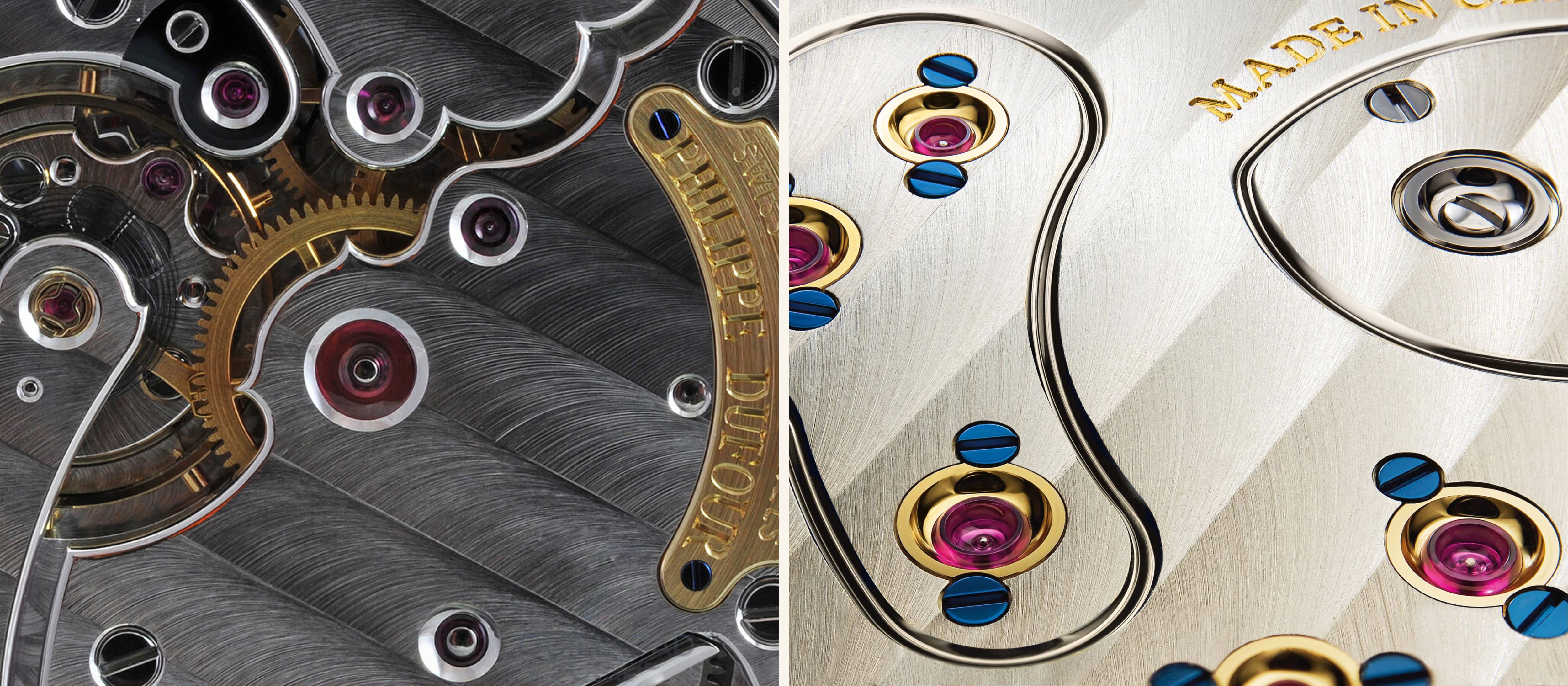
Skeletonization / Open-working
The terms skeletonization and open-working are often used interchangeably. The techniques, although similar in approach, vary in execution. Skeletonization is a process referring to displaying the inner-workings of a watch’s movement through openings in the dial as well as the movement components. A skeletonized movement is intended to be like that from the beginning with the parts born hollow. Such a decoration entails a “see-through” aesthetic to the timepiece with the inner mechanics on display. Very often, skeletonized movement components feature elaborate engravings and sustain as the finest examples of haute horlogerie execution.
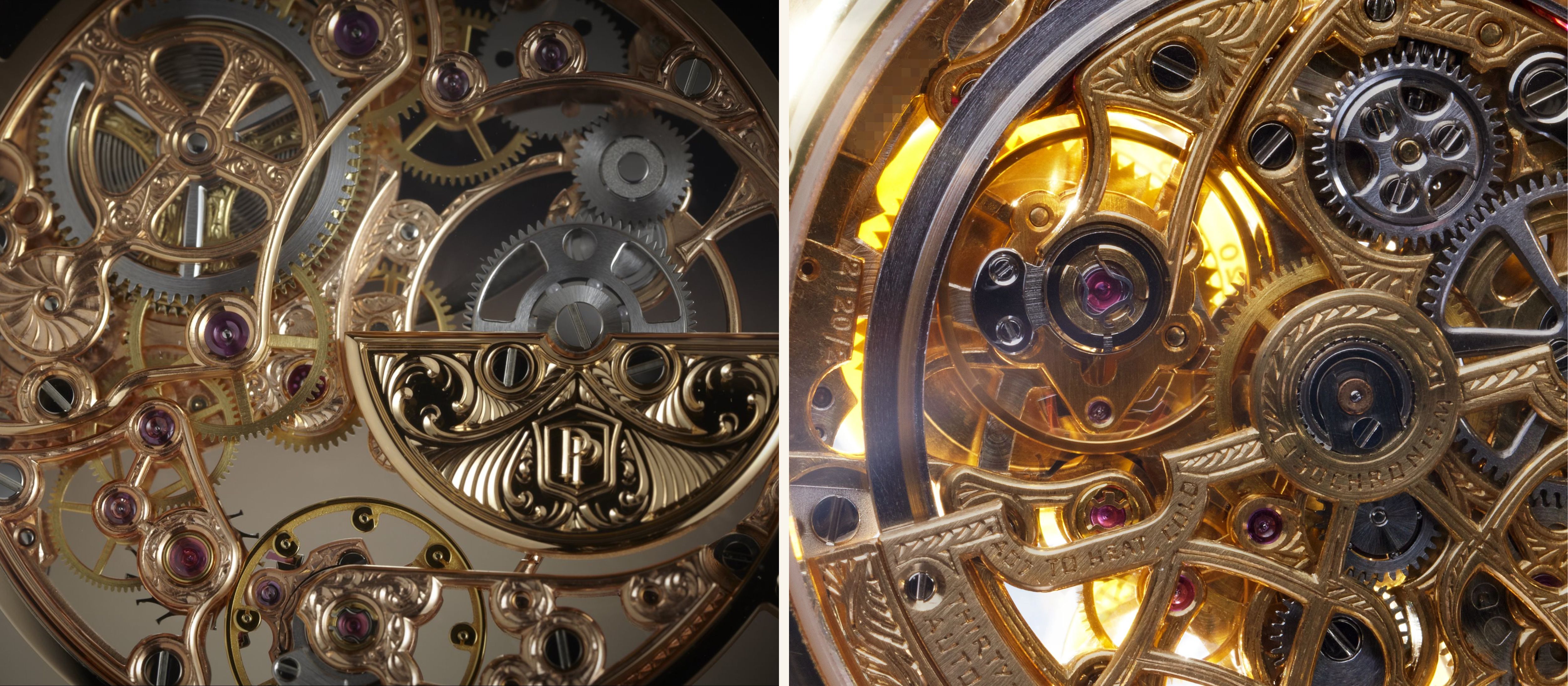
Open-working on the other hand is executed as a redundant carving of a normal caliber’s bridges and plates leaving only the bare structural minimum to support various mechanical components. A regular movement’s parts get sawed and filed into hollow shapes and the process is referred to as open-working. Both skeletonization and open-working have little to no positive effect on the functioning of a watch with the execution reserved for pure decorum.
Striping
In many regards, the Côtes de Genève or Geneva striping exists as a signature decoration in watchmaking. It’s maybe because the execution of this technique is easily comprehensible as it spans a comparatively wider area by surface. Moreover, its occurrence is much liberal for watches across all price points with anything from a sub $1,000 Tissot to a $135,000 Rexhep Rexhepi Chronomètre Contemporain featuring striping, although in significant variance of executional finesse. Côtes de Genève, often referred to as Geneva waves or stripes, is typically applied to bridges. It creates the elegant effect of an undulating parallel pattern that plays with light, evoking the gentle movement of waves. The earlier executions of Côtes de Genève had a functional intent as the tiny grooves forming the waves could catch dust and mechanical debris that would otherwise risk clogging the moving components.
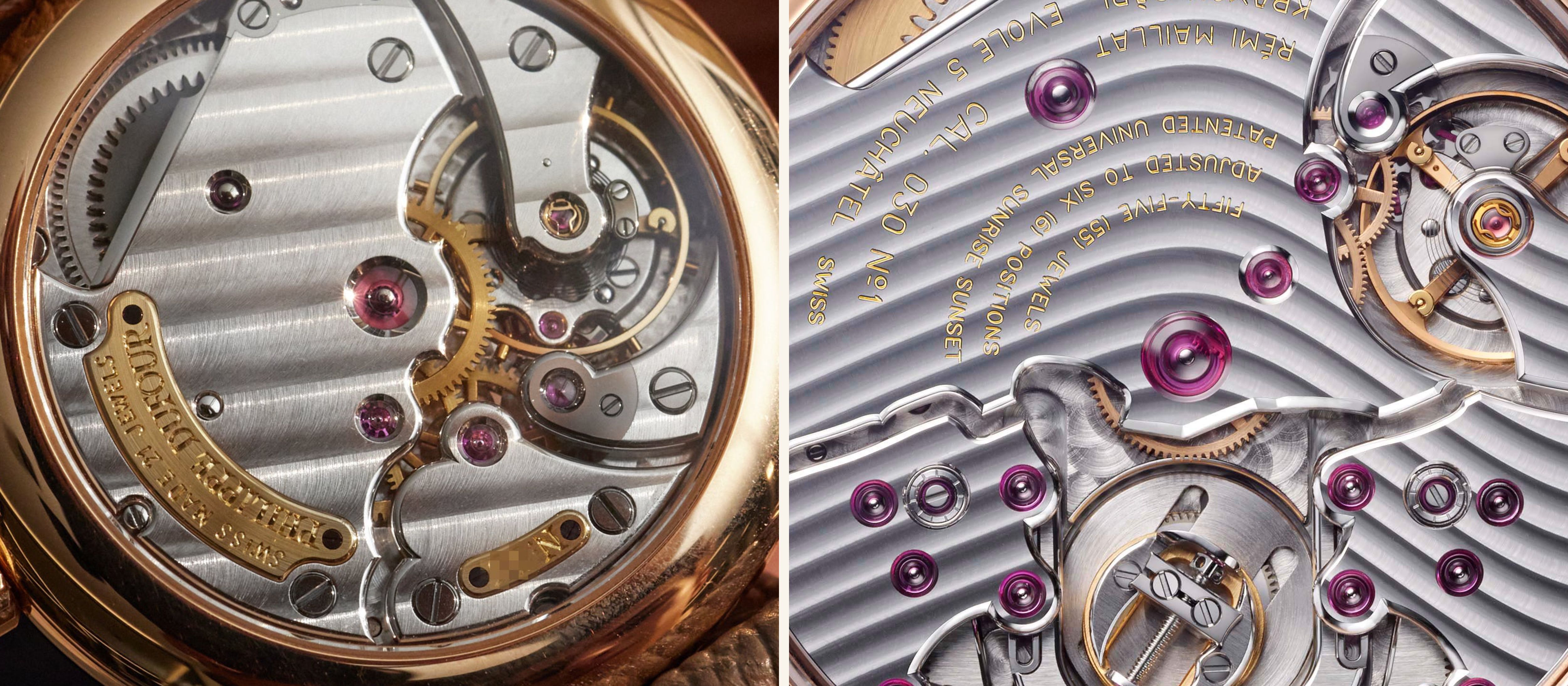
To realize these wave-like patterns set in parallel quarter-circles, a high rpm rotating tool is moved across a plain surface to scratch it. Immense care is required to maintain consistent depth and width of the waves in the traditional execution of this decoration. The technique adopted for the mass-produced and lower-end spectrum of the products is performed on a CNC for speed and scale. A notable example of Côtes de Genève can be found in the creations of Remi Maillat. His Krayon Anywhere features a parallel but non-linear execution of striping lending it a more free-flowing appearance. It stands as a masterful exercise in classical finishing with a nuanced approach.
Finishing Touches
And there you have it, folks! From A for Anglage all the way up to Z for Zaratsu, actually more like S for Striping, we’ve covered it all. After four parts of this alphabetical exploration of watch finishing and decoration techniques, you're now very much qualified on the discipline. And for that, you have my sincere applaud. As we’ve been learning what we’ve learnt, it lends to a strange realization that many times in watchmaking, the solution isn’t always the most technically advanced but rather the most aesthetically attractive. Also, the idea of a good watch, even a great watch for that respect, isn’t only confined to a finely finished timepiece.
In the end, when executed in the traditional way by hand, not every anglage is similar nor is every cloisonné enamelled surface. The hand lends a unique execution which can never be replicated, even by the same hand. Does that mean there are a thousand variations of anglage and many more of cloisonné? Not necessarily. But the sentiment of distinctiveness and singularity is strong with all that’s crafted from hand and that remains to the eternal credit of fine watchmaking. And on that subject, your aptitude is clearly cultivated. Also, your watchmaker’s loupe is due a delicate pat.
No articles found